Table of Contents
Report
Mushroom farm
Author(s):
- Erendiro Pedro
- Alex Winter
- Julia Slasko
- Julien Battaglini
- Maike Fälker
- Ronald Kivipelto
Acknowledgement
The team would like to thank ISEP and the EPS supervisors for the opportunity to take part in this great learning experience. They would like to give a special thanks to professor Abel Duarte and the microbiology technicians for their help and support.
They would also like to give a special thanks to INESCTEC for providing an area to test our cultivation process.
Glossary
Abbreviation | Description |
---|---|
ANIPLA | Associação Nacional da Indústria para a proteção das Plantas |
API | Application Programming Interface |
CAGR | Compound Annual Growth Rate |
EPS | European Project Semester |
ISEP | Instituto Superior de Engenharia do Porto |
INESCTEC | Institute for Systems and Computer Engineering, Technology and Science |
USB | Universal Serial Bus |
LED | Light Emitting Diode |
PE | Polyethylene |
PP | Polypropylene |
PVC | Polyvinyl chloride |
- Introduction
- Presentation
The team is made up of 6 interdisciplinary students from 6 different nationalities. The team has come together to be part of the European Project semester (EPS) in the spring of 2019 at Instituto Superior de Engenharia do Porto (ISEP). Over 5 months (1 semester) the team is going to use each other’s knowledge from various backgrounds and strengths to work on creating a sustainable mushroom farm using coffee waste. This highly motivated and passionate team is shown in Figure 1 and composed by: Alex Winter, a Product designer student from Switzerland, Erendiro Pedro, an Angolan electrical and computer engineering student, Julia Slasko, a business and technology student from Poland, Ronald Kivipelto, a electrical engineering student from Estonia, Julien Battaglini, a general engineering student from France, and Maike Falker, a media technology student from Germany.
- Motivation
The team’s motivation behind choosing the project to build a mushroom farm using coffee waste was that although everyone comes from different background, none of the team members had directly worked with food production. The team could agree that the food industry produces a lot of waste. The team was henceforth motivated to create a sustainable food system, which encompasses sustainable, social, environmental and economical concepts. The project would allow to spread awareness and encourage environmentally friendly practices. The whole team was directly interested in the delicate process used to cultivate mushrooms, how it could be optimised and spread widely. The idea allowed everyone to use their specific discipline/skills in a totally unique and new situation broadening their understanding in not only their field but how their field can be applied to new industries. The team also took this opportunity to develop their skills in project management, soft skills and ability to work as a team.
- Problem
Coffee is a massive industry, with more and more people consuming coffee, the negative environmental impacts from the industry keep growing. When coffee is made only less than 1 % of the biomass ends up in the cup [1], with almost 10 million tons of coffee consumed each year [2]. A huge amount of energy and resources go into producing and shipping coffee beans around the world however all the value is placed on the liquid extraction of their flavour. The problem is that 99 % of the biomass from the coffee is wasted [3]. This vast amount of coffee waste is full of nutrients and cellulose, which makes it an excellent substrate for grey oyster mushrooms to grow in. Mushrooms play a crucial role in the cycle of nutrients and their ability to do this makes them perfect for recycling a wide range of organic waste streams. Grey oyster mushrooms, in particular, are very versatile and have shown to grow on over 200 different agricultural waste materials [4].
- Objectives
The main objective is to develop a sustainable service by which coffee waste is collected and then used as a growing medium for grey oyster mushrooms. The process will be made as sustainable and efficient as possible. This will be done by developing a grow kit with a monitoring system, which allows the observation and optimisation of the growing environment; enabling the mushrooms to thrive and grow in abundance. The aim of the overall image and values of the company is to promote sustainable food production and to connect people back to the food they eat. This is to stimulate a more environmentally friendly mindset. A service will be aimed at a local market whereby local economy is supported by sourcing, producing and selling within the local market. Surrounding the whole project, the team aims to develop multidisciplinary skills, as well as soft skills, such as project management and communication skills.
- Requirements
The project has the following requirements:
- Automatic monitoring and control of the chamber conditions
- The medium or small scale of the device
- Usage of low-cost hardware solutions (Not exceed the budget of 100 € for the construction of prototype)
- Usage of the open source software
- Adaptation of the International System of Units (NIST International Guide for the use of the International System of Units)
- Comply with the following EU Directives:
- Machine Directive (2006/42/CE 2006-05-17) [5]
- Electromagnetic Compatibility Directive (2004/108/EC 2004 12 15) [6]
- Low Voltage Directive (2014/35/EU 2016-04-20) [7]
- Radio Equipment Directive (2014/53/EU 2014-04-16) [8]
- Restriction of Hazardous Substances (ROHS) in Electrical and Electronic Equipment Directive (2002/95/EC 2003-01-27) [9]
- Functional Tests
To ensure the proper functioning of the prototype, the sets of tests presented in Table 1 will be performed:
Test cultivation Process | Sensors/Actuator Test | Hardware Testing | Software Testing | Material analysis |
---|---|---|---|---|
Sterilization of Coffee waste | Humidity control | Power Supply Circuit Test | Sensor Functionality | Material Simulation |
Incubation period | Temperature Control | Sensor Functionality | Actuator Functionality | FEA Analysis |
Fruiting Period | Airflow control | Actuator Functionality | Integration of sensors | Chemical/Aqueous resistant |
Harvesting Process | Full system Functionality Simulation | |||
Waste Management |
- Project Planning
The project is coordinated according to agile project management in terms of scrum methodology. Scrum is an agile project management methodology or framework used widely for software development projects with the aim of delivering new software capability every two or four weeks. The approach articulates a set of values and principles to guide decisions on how to develop higher-quality software faster. Nowadays, not only is it used for software development but also it has spread to other projects, such as IT and marketing, where the speed of work is high in the presence of complexity and ambiguity [10].
The main advantages of this concept are:
- Higher productivity
- Better-quality products
- Better team dynamics
- Reduced time to market
- Improved customer satisfaction
The Scrum framework is shown in Figure 2:
- Report Structure
The project is structured in eight different chapters as shown in Table 2.
Task | Title | Description |
---|---|---|
1 | Introduction | General introduction of the team, the motivation and the objectives of the project |
2 | State of the Art | Research of existing solutions and products on the market in terms of scientific and commercial aspects |
3 | Project management | Documentation of the progress in accordance with the concept of the agile management method SCRUM |
4 | Marketing plan | The brief description of the market analysis, on what is built a marketing strategy consisting set of actions to implement it |
5 | Eco-effciency measures for Sustainability | Set of necessary components such as design, tests, and calculations in order to make the project sustainable |
6 | Ethical and Deontological Concerns | Analysis of the ethical challenges, limitations and their possible solutions |
7 | Project Development | The architecture, components and the functional tests of the prototype |
8 | Conclusion | Summary of the results and possible future development |
- State of the Art
- Introduction
In the State of the art, the natural growing process of mushroom is going to be discussed, along with the different existing solutions, for industrial and individual purposes.
The state of the art refers to the highest level of general development, as of a device, technique, or scientific field achieved at a particular time. This is done to get ideas and solutions that could be added to the product or business plan. The cultivation process will be investigated in a lot of detail to gain a much richer understanding of the process, to see if any areas can be optimised or simplified to allow people to grow their own mushrooms as well as producing them on a more industrial scale.
By gaining a deeper understanding of not only the cultivation process but also the market allows detailed analysis of potential gaps in the market leading to a particular niche to be capitalised on.
The primary goal of a mushroom farm is to produce a consistent yield of mushrooms to be sold on the market. The goal of this report is to investigate the feasibility of creating a business surrounded by the idea of growing mushrooms using coffee waste. The output of the business needs to be investigated through market research, however the vision of the business is clear. To connect people back to their food through sustainable food production. This will either be done by creating a sustainable mushroom farm that supports the local economy, local environment and local people, or by creating a service that allows people to learn and grow their own mushrooms at home, thereby reconnecting them with the food they eat and how it is produced.
- Presentation of Oyster mushroom and its growing process
- Oyster Mushroom (Pleurotus Ostreatus)
Because the business is based around growing mushrooms in coffee waste, the mushroom best suited to do this is the Oyster mushroom. Coffee has loads of cellulose in it which is essential for the cultivation of Oyster Mushrooms. The common name Oyster refers to multiple species of mushrooms including Pleurotus pulmonarius, Pleurotus salmonostraminus, Pleurotus djamor, Pleurotus citrinopileatus, Pleurotus ostreatus, Hypsizgus ulmarius, and others. These mushrooms come in a range of colours, size and texture. Oyster mushrooms can come in pink, blue, brown and white. This allows small scale growers to cultivate 4 or 5 different products with growing oyster mushrooms. Oyster mushrooms are native to the North-eastern US. Most of the strains of Oyster mushrooms can be cultivated using the same system and growing process, all that differs is the spawn used, meaning only one method of cultivation needs to be mastered in order to produce an attractive assortment of different oyster mushrooms. In the image below you can see a large variety of different oyster mushrooms available on the market.

- Mushroom growing process
Oyster mushrooms are basidiomycetes, referring to their method of sexual reproduction. The gills on an oyster mushroom contain basidia (microscopic structure). Attached to the basidia are 4 haploid spores which are released into the air at maturity. These spores germinate into mycelium. The mycelium grows through its food, in this case coffee and eventually fruits a mushroom providing the growing conditions are suitable. Oyster mushrooms are known for their heavy spore count and therefore routine cleaning in the fruiting room/environment is crucial. The goal of the mushroom is to provide a platform for sexual reproduction and release of the spores. Humans, insects and animals are part of the chain which spread the spore of the mushroom [13] Mycelium continually breaks down food using an enzyme. These chemical enzymes contain antimicrobial compounds which create a protective barrier around the mycelial network. Fungi digests externally and then absorbs nutrients that have been broken down into its body. These enzymes break down food like lignin and cellulose (both found in coffee) into simple sugars which are used for continued mycelial growth. This is know as the colonisation of mycelium or the incubation period after inoculation has occurred [14] It is crucial to have a solid understanding of mycelium because this is what mushrooms fruit from. Without healthy cultivation of mycelium, fruiting of the mushrooms will not occur. A mushroom farm firstly needs to cultivate mycelium and then through the maintenance of the right conditions (high moisture, high oxygen and the right temperature) will cause mushrooms to grow. Paying close attention to the health and growth of mycelium will help to achieve bigger yields. Mycelium needs to be cultured in a petri dish, this single petri dish is the starting point to produce large quantities of mushrooms. Different strains can be cultured to meet the needs of the growing. After the mycelium has been fully colonised and the right conditions are met for fruiting to occur, mushrooms will mature within a week. At this point, they are ready for harvesting. Each cake of block of colonised mycelium will produce between 3 to 4 flushes of mushrooms. After the 3rd or 4th flush of mushrooms, the remaining mycelium can be recycled by adding more substrate (food) and allowing it to colonise again so fruiting can occur. The Consistency of all these methods is the key to success [15].
Growing Mushrooms in coffee.
Mushrooms are notoriously hard to grow because of inconsistent results. This is partly due to the mass production of low-quality grow kits which give unreliable results. Even in the wild mushroom’s growth is very unpredictable. However, by using the correct knowledge and relatively simple techniques it is possible to cultivate mushrooms on both an industrial and home scale. Similar to the fruits produced by a tree, mushrooms are the reproductive fruits of a dense rootlike network of cells known as mycelium. When mycelium runs out or it’s put under some type of environmental stress it switches into survival mode and produces mushrooms in order to release its spores into the wind to find a better place to live. Lucky for us it is possible to recreate and manage the life cycle in order to cultivate good crops of edible mushrooms. Mushroom farming heavily relies on very strict growing conditions and minimising competition through pasteurisation [16]. However, this can cost quite a lot for someone who wants to grow at home. One of the aims is to make it as cheap and rewarding as possible. For this reason, Oyster mushrooms are a great place to start as they are very resilient and can grow in many types of agricultural waste. The most common materials used to grow Oyster are freshly cut hardwood logs or straw. Growing on logs can be quite difficult and can take several years before your first harvest. Growing on straw requires pasteurisation to kill off any micro-organisms that will compete with mycelium. Growing in coffee has quite a big advantage as it has already been pasteurised by the brewing process meaning it is ready for inoculation, skipping out the pasteurisation step. Not to mention used coffee grounds are a massive wasted resource as they are still full of nutrients which Oyster mushrooms love to grow on.
Inoculating
Firstly the mushroom spawn needs to be ordered. You will have greater levels of success if you use high spawn to coffee grounds ratio. To start 500 g of Oyster mushroom spawn to each 2.5 kg of used coffee grounds [17] Inoculation can be done in filter bags or buckets to provide a perfect growing environment and to prevent chances of contamination. Bags will have a filter and containers will have small holes.

Coffee collection
In order to skip out pasteurisation step, the waste coffee needs to be fresh that day and therefore a service will be created to collect fresh coffee waste. Once the coffee waste is collected fresh, with very sterile conditions the coffee has to be mixed with the mushroom spawn and then added into the cultivation bag/container. Ensure there are small air holes if a container is being used instead of a filter bag.
Spawn Run
Place container in a warm (18-25°C) and dark place. During the next 3 weeks, the spawn will come to life and colonise across the coffee grounds, turning the mixture white [19].
Fruiting
After about 3 to 4 weeks the whole container of coffee and spawn mix should be completely white. If you see any other colours such as green or black, then this is a competitor mould and needs to be removed. Salt can be used to kill it off without compromising the mycelium. This is why hygiene is so crucial. If you have achieved a nice white container then the mycelium is ready to enter the fruiting process by which you get mushrooms. Place the container in a pot with plenty of fresh air and a little light. Mushrooms love humid conditions so it is important to spray the mushrooms so they do not dry out [20] After a week or so you will see mushroom pins start to develop. Over the next 5/7 days, the mushrooms will double in size every day. When the edges of the cap start turning upwards it is time to harvest. Cut the mushrooms at the base and be sure to remove the whole mushroom. You will typically get 3 or 4 flushes. The remaining mycelium can be used as spawn for the next grow.
- Existing solutions for individuals
Mushroom kit
A substrate is already inoculated with mycelium and wrapped into plastic. Wrap is then placed inside the box, which is relatively small and allows to grow mushrooms anywhere in a home. Consumer has to cut an opening into the package and sprinkle it with water on a daily basis. After some time mushrooms will start to grow. After harvesting the process can be repeated twice.
Examples of existing mushroom grow kits are shown in Table 3.
Strenghts of grow kits:
- Easy to use
- Customers gain knowledge through the process
- Mushrooms are fresh
- Grow kit is easily recyclable
Weaknesses of grow kits:
- They are not designed for sustained cultivation of mushroom
- Only around 3 small flushes can be harvested
- Existing industrial solutions
Aromas & Boletos
A company that focuses on the enhancement of sustainable and ecological production of wild and exotic mushrooms. Products and services for mushroom cultivation are developed and marketed. In laboratories, modern techniques are used to produce mycelium and substrate. An array of products includes mushroom spawn, grow kits, lab supplies, mushroom production equipment, and gourmet mushrooms. In the area of research, innovation and development Aromas & Boletos strives to innovate the production of mushrooms. They also do workshops for producers and aficionados, show-cookings, tastings and other activities in nature [25].
Cogumelos Cultivados Lda.
A company that is specialized in the production, commercialization and distribution of exotic mushrooms. All the production is done in a biological way, focusing only on the national market. Sales are made directly to the customers such as restaurants & hotels, shops and markets, and some supermarket chains. The mission is to be an asset in the Portuguese food market and to offer high-quality biological products at affordable prices [26].
Floresta Viva
Floresta Viva is responsible for the appearance of new producers, through specialized training for the activity with participants from all over Portugal and the Islands, Spain, India and France. The company is committed to being a valid partner of the producers, to be an active part in the propagation of the consumption of biological products of high-quality control. Their services include monitoring and technical support for mushroom producers, workshops on the production of mushrooms, commercialization of mushroom of different species. Other services are production and distribution of inoculated wood, as well as commercialization of specific machines and tools for shiitake trunk production [27].
- Conclusion
Mushrooms grow in wild and some of them can be grown on both a domestic and an industrial scale. While farming is nothing new, people are demanding more sustainable foods. People not only want healthy food but want to know that it has been cultivated in a sustainable manner and is not having a negative effect on the environment. People are willing to pay slightly more for organic and healthy products and this is why more and more people are growing their own food at home. There are so many benefits of growing at home. Firstly, it almost eliminates the distance between the farm and the consumers plate, which significantly lowers the carbon footprint of the food and guarantees freshness. Cultivating food at home can be educational and can connect people back to the food they eat. Many people do not have access to growing spaces and are sometimes unable to grow at home, but this is what makes growing mushrooms so great. Growing mushrooms does not require a lot of space and can easily be done inside. Domestic cultivation of fungi has been popularized by grow kits, they are easy to use, take little space and after using are easily recyclable, however, there is a major disadvantage, these kits only produce three flushes and are not normally very big. After this, a new kit has to be bought or can be re-cultivated but normally can be quite time consuming and requires some specialized equipment, which can be costly for home growers. Cultivating mycelium can be difficult at home because it needs very sterile conditions. People want something that allows them to cultivate mushrooms in a sustainable way but does not require excessive effort or money. A potential solution could be to establish a service that collects fresh coffee waste and inoculates it with mushroom spawn, people would be able to buy fully inoculated mycelium made from fresh coffee, allowing them to grow mushrooms on a decent scale. The remaining part of the process is relatively easy. The company, could supply customers with a monitoring device to make growing as simple as possible, as well as providing all the resources and information needed. The company could also provide courses to teach people about cultivating mushrooms and sustainable foods. Other option could be to build a mushroom farm by which the company provides consumers and restaurants with fresh organic mushrooms grown from coffee waste. As there are already existing farms, which have a strong position in the market, it would be extremely difficult for an EPS team to compete with established competitors. The team decided somewhat to combine the two ideas and build a device, while also providing the service mentioned above. The service would also include the collection of coffee waste from partnering restaurants and coffee shops.
- Project Management
- Scope
The first step of successful project management is the creation of scope in order to define and organize the work that has to be executed by the project team. The best idea is to use a simple hierarchical decomposed structure of all tasks and deliverables which are essential to accomplish the final project outcome. One of the widely used structures is a Work Breakdown Structure (WBS), which visually divides the scope into sections, where each of them provides further definition and detail. In Figure 5 it is presented a brief WBS structure of mushroom farm project.

- Time
After making scope, the second step of planning is managing work time. The project is coordinated according to agile project management in terms of scrum methodology but is always better to prepare general overview with milestones and phases in the project, that is why the Gantt chart has been created. The Gantt chart is divided into phases based on project scope. The chart is a more classical tool for monitoring the course of events and tasks completion, but it could be helpful in terms of monitoring and preparing sprint backlog. The Gantt chart of mushroom farm project is shown in Figure 6

- Cost
Six students were working on a mushroom farm project. Work consisted of tasks related to research, planning, management, project development, etc. In order to estimate cost of labour, hours spent on work by each student were multiplied by hourly rate of 5 €. The estimations are shown in Table 4.
Name | Time [h] | Hourly rate [€] | Cost [€] |
---|---|---|---|
Julien | 118 | 5 | 590 |
Alex | 115 | 5 | 575 |
Julia | 115 | 5 | 575 |
Eren | 112 | 5 | 560 |
Ronald | 111 | 5 | 555 |
Maike | 77 | 5 | 385 |
Total cost : 3240 € |
---|
Complete list of prototype components and their total cost is shown in Price Analisys section in Table 29.
- Quality
As Waste to Fungi is a business based around food production, quality has a very important role to play as the final product will be consumed. When it comes to food there are certain health regulations that need to be met.
Food quality: To minimise the risk of serious health consequence or even death from consumption of contaminated produce, the Food and Drug Administration (FDA) have established a science-based minimum standard for safe growing conditions, harvesting, packing and holding of produce for fruits and vegetables grown for human consumption. FDA is proposing these standards of the FDA Food Modernization Act (FSMA) [28].
Usage Quality: Before going to market the grow kits and surrounding procedures need to be functionally tested and optimised to ensure high-quality yields. The benefits of growing at home must subside the befits from buying directly from supermarkets. The procedure must guarantee freshness, cost-effective yields and simplicity in the cultivation process. Quality of procedure will be monitored with sensors to ensure the highest quality growth is achieved.
Service Quality: Service quality surrounding the sale of the grow kits is crucial. Besides providing information for the maintenance of the grow kit at home the business intends to provide a coffee collection service. Business must ensure that there is good communication between suppliers of coffee waste and ensure the proper care and treatment of coffee waste is conducted to avoid any contamination before the cultivation process begins. The business aims to reconnect people back to the food they eat by supplying educational workshops and information around the idea of cultivating mushrooms and circular economy. Information and workshops must be of high standard and must be reliable. This will help the success of spreading awareness.
Description | What ? | How (much) ? |
---|---|---|
Internal & Work Ethics | ||
Finances | Budget | maximum 100 € |
Logistics | Local | 50 km radius around Porto |
Electronics | ||
Sensors | Humidity accuracy | +/-3% |
Sensors | Temperature accuracy | +/-0.5 °C |
Sensors | Humidity range | 0-100% |
Sensors | Temperature range | 0-40°C |
Power | Low Power consumption | Overall: < 50 Watt |
Overall | Comply with EU directives | Health, Low voltage |
Raw Materials | ||
Coffee | Freshness | maximum 24 hours |
Spawn | Quality | Trusted supplier |
Spawn | Quality | Store at 4°C |
Process | ||
Sanitary | Safety | Sterile environment |
Sanitary | Safety | Routine cleaning of equipment and environment |
Sanitary | Safety | Follow safety regulations |
- People
Responsibility Assignment Matrix is used to identify roles of members in a project team. Matrix is a table that provides an overview of what tasks should be done by whom, while also pointing out responsible person for each task [29]. The companies task allocation is shown in Table 6.
Description of symbols used in a table:
- R = Responsible (Person who is mainly working on the assigned task and bears responsibility of completing it)
- P = Participant (Person who has the supporting role in assigned task)
- A = Accountable (The one who ensures that prerequisites of the task are met and who delegates the work to those responsible)
- C = Consultant (Subject matter experts, whose opinions are sought) [30]
Task/People | Eren | Alex | Julia | Julien | Maike | Ronald | Supervisors |
---|---|---|---|---|---|---|---|
Task identification and allocation | R | A,C | |||||
Gantt chart | R | A,C | |||||
Blackbox diagram | P | R | A,C | ||||
Technical research | P | P | P | A,C | |||
Market research, existing products | P | R | A,C | ||||
Initial budget planning | R | A,C | |||||
Specific plan | R | A,C | |||||
Business plan | R | A,C | |||||
Final schemes, diagrams | R | P | A,C | ||||
List of materials | P | P | P | A,C | |||
Interim presentation | P | P | P | P | P | P | A,C |
Interim report | P | P | P | P | P | P | A,C |
Prototype construction hardware | P | P | R | A,C | |||
Prototype construction software | R | P | A,C | ||||
Prototype assembly | P | P | P | P | A,C | ||
Prototype functional tests | P | P | P | P | P | P | A,C |
Final report | P | P | P | P | P | P | A,C |
Video | R | A,C | |||||
Poster | R | P | A,C | ||||
Manual | A,C |
3.7 Communications
Such a multidisciplinary and diverse project as this one would be impossible without good communication. It is necessary both to ensure that all members have the opportunity to express their convictions, thereby increasing positive discussions and diversity of opinions, or to ensure that problems that arise are dealt with appropriately. On the other hand, poor communication can worsen time management, deteriorate the team's relationship among many other problems. Communication is one of the pillars of a good project.
In order to promote good communication in the team, a policy of transparency and honesty has been adopted that allows each member to express their opinion in a judgment-free manner, but subject to constructive criticism, so no problem is left under the rag and the discussion of ideas is encouraged.
In terms of direct communication (in person), meetings are held every day to find out the progress made so far, as well as weekly meetings where a situation is made, and a reassessment to the team's planning and objectives. Moreover, on Thursday of each week, a meeting with a supervisor is organized that allows the Team to have an external opinion, to improve research, find new solutions and better organize.
As direct communication is not always possible, alternative communication channels have been created in social networks where it is possible to maintain contact, share documents or any other type of relevant information to the project. The great disadvantage of these means is that compared to direct communication, it is more difficult to ensure that the messages are not being misunderstood, so as to mitigate that effect was agreed between the team that very important matters relating the project would only be discussed in person. The great advantage of these means of communication is that they are easy to reach, very practical and allow the contact to be maintained even when the team is far away.
The main alternative communication channels used are:
- Facebook Messenger
- Whatsapp
- Google Drive
- Gmail
The communication matrix is displayed in Table 7 .
What | Why | Who | When | To whom |
---|---|---|---|---|
Deliverables | Development of the project | Team member in charge of the task | On the deadlines | Supervisors and the Team |
Daily Stand-ups | Have an overview of what each group member has done so far, what were the biggest difficulties, and what is going as planned, as well as implement strategies to solve the problems faced. | The Team | Every weekday | The Team |
Agenda | Informing the supervisors about the content of the meeting | Team member in charge of the task | 24h before the meeting | Supervisors |
Weekly meeting with the supervisors | Evaluating the progress of the project and having counseling on the ideias propozed | Supervisors and the Team | Every Thursday | Supervisors and the Team |
Weekly team meetings | Make an analysis of the progress made and make a reassessment of the planning so far | The Team | Every week (on the most convinent day for every member) | The Team |
3.8 Risk
Managing risk is a useful tool for measuring the impacts of tasks, measuring project fissibility, and generally planning more carefully. Without good risk management, there is no good way to come up with good alternatives for problems that may arise, so there is no way to control the impact that the tasks have on the project.
Good risk management requires identifying, analyzing and assessing all the possible risks.
In Table 8 is presented a description of the risk, its causes and effects, control mechanisms, the response strategy, and the rank.
Note:
Low = 1, Medium = 2, Strong = 3.
The Rank number comes from the multiplication of the impact and the probability.
Explanation of strategies:
Accept: Accepting the risk and do nothing.
Transfer: Transfer the risk to someone else.
Avoid: Eliminate the risk.
Mitigate: Decreasing probability or impact.
Description | Cause | Effect | Trigger | Response strategy | Impact | Probability | Rank |
---|---|---|---|---|---|---|---|
Internal risk | |||||||
Teamwork disagreements | Misunderstanding. Problem of communication. | [Time] Efficacy of the work. Delay of work | Differences of opinions. Bad communication | [Mitigate] Try better comunication practises. [Accept] | 1 | 2 | 2 |
Team member missing | Sickness, irresponsability, accident | [Time] Less working capacity, less diversity of opinions | Lack of commitment / sense of responsability | [Mitigate] Encourage/Motivate team members for the project. [Mitigate] Promote organization and responsability [Transfer] Change the responsibility of the tasks to another team member. | 2 | 1 | 2 |
External risk | |||||||
Late delivery of materials | Suppliers didn't hold the delivery time. Transportation strike. No stock. | [Time] Impact on the time delay and the development of the product | Tracking the transportation online | [Avoid] Order components as soon as possible and verify transportation | 3 | 2 | 6 |
Incorrect components are delivered | Suppliers behaviour, verification | [Time]/[Costs] Increase time delay in the development of the prototype, and costs. | Checking the feedback of suppliers and order acknowledgement of receipt | [Mitigate] Send back and order new components. | 3 | 1 | 3 |
Technical risk | |||||||
Non-functional components | Bad component quality, Broken component | [Scope]/[Time]/[Costs] The product will not work. Impact on the time delay and costs | Checking the history/reliability/reviews of the suppliers | [Mitigate] Negotiate with supplier and claim the guarantee to replace the defective component. [Transfer] Have alternative suppliers. | 3 | 2 | 6 |
Software not working | Bad algorithm selection. Bug. Lack of knowledge. | [Time] Programming again. Impact on the time delay | Not testing constinuosly the code. | [Avoid] Change programme. Testing constinuosly the code. Redesign code. | 3 | 2 | 6 |
Growing process not working properly | Bad implementation of the process. Process selected not apropriated | [Time]/[Costs] Time delay (deadlines). Delay or inviabilitate of prove of concept. Mushroom not eatable | Not testing process carefully. Not selecting the right process. | [Avoid] Test the process several times before implementing in the device. Change process | 3 | 1 | 3 |
Final prototype not working | Software problems. Hardware problems, Wrong implementation | [Scope]/[Time]/[Costs] Time delay (deadlines). Final device does not work, can't be tested. | Not testing continuosly the device in each stage | [Avoid] Make several tests during the development, and test each sensor and actuator separetly. Buy other components, redesign the device. | 3 | 1 | 3 |
Risk assessment Evaluation
After completing many of the tasks, some things in the risk assessment were overlooked and the probability of occurrence was underestimated. There were 3 main risks where the probability should have been higher to reflect more realistically what happened. First of all, the probability of a team members missing should have been set to 2 instead of 1 moving the ranking to 4 instead of 2. The team underestimated the risk of team members not being present. The team should have created a more detailed calendar so team members could plan for missing team members and compensate accordingly. The team also agreed that work should be done collectively rather then working independently at home. When the team worked collaboratively, productivity and communication was much better and resulted in a higher standard of work.
This risks associated with the growing process were also underestimated. Probability should have been set to 3 instead of 1, bringing the ranking up 9. This would be a much more realistic reflection of how the process went. None of the team members had cultivated mushrooms before and should planned for higher probability of risk. In reality the team had quite a few issue with cultivation. Many of the buckets were contaminated which resulted a big reduction in the final yield and creating many time lags. The team has since then refined the process and results are promising, however the team is now behind and should have given more time for cultivation to account for time lags.
Lastly the team underestimated the probability of final prototype not working. Probability should have been set to 3 instead of 1, bring the ranking up to 9. Probability could have been lowered with better planification of building and testing the prototype. The team members had issues with trouble shooting the electronic monitoring system. This created time lags which had a cascading effect on the recording and monitoring of the cultivation process. This could have been avoided with better planification of building and testing the system and with a better estimation of probability of occurrence.
- Procurement
Managing Procurement properly can support purchasing goods and services from external suppliers in the most efficient way. Quality and costs of goods as well as costs related to postage are crucial aspects to keep in mind while developing a procurement strategy. As there is a variety of potential suppliers in the market, materials could come from any website or local shop.
For the project to be efficient and successful, use of the supplier relationship management will be made, also known as SRM. This is a strategic and segmented approach, executed on the entire supply base, to maximize value and minimize risks [31].
The SRM method contains the following five steps:
- Step 1 – Supplier identification: The first step in the SRM method is supplier identification. The company must sort out and identify all its suppliers, to whom they paid invoices over a certain period.
- Step 2 – Supplier segmentation: This is an important step. The long list of suppliers to whom invoices have been paid must be segmented. Segmentation helps to find those suppliers that are capable of contributing to the business strategy. Only these, limited number of suppliers are worth the time and effort to build a close relationship and partnership, with.
- Step 3 – Relationship analysis: Mainly for the top segment of suppliers classified as interesting to build a partnership with, the company must determine the existing relationship type. This is realized by using the supplier relationship analysis tool.
- Step 4 – Relationship management: Mainly for the top segment of suppliers the existing relationship type needs to be managed towards the ideal relationship type, which is the leverage-core relationship type.
- Step 5: – Evaluation: On a regular basis the SRM results and lessons learned need to be documented and evaluated. This will lead to a series of recommendations towards the business like integrating the top segment suppliers for new research and development activities or proposing to restart step 2, the supplier segmentation [32].
- Stakeholders Management
Stakeholders are independent parties which have an interest or concern about something. In this case an interest for the project of creating a mushroom related business.
In order to manage them, a stakeholders management analysis through two different tools has been made:
- A stakeholders analysis table represented in Table 9
- A stakeholders analysis matrix represented in Figure 7
N° | Who | Role | Influence | Interest |
---|---|---|---|---|
1 | Team | Developers | High | High |
2 | Supervisors | Controllers | High | High |
3 | ISEP | Sponsor | High | Low |
4 | INESC TEC | Sponsor | High | High |
5 | I3S | Sponsor | Medium | Medium |
6 | Suppliers | Providing materials | Low | Low |
7 | Competitors | Competition | Low | Low |
8 | Consumers | Buying the product | Low | Low |
With the help of these tools, more effort needs to be put in informing the sponsors and supervisors on the evolution of the project since they are the Key Stakeholders. Adapting to communication concerning other stakeholders depending on the evolution of the project and of their place and interest in our product is also important.
- Sprint Outcomes
In this section, the sprint outcomes is put available through the Table 10, which details the tasks completed throughout the sprints and the velocity achieved. Sprints and their outputs and reviews are an essential part of the scrum project management method that will be used for this project.
PBI | Assignee | Planned Effort | Completed | Not Completed |
---|---|---|---|---|
Sprint 3 - 21/03 to 27/03 | ||||
ID009 List of Materials (what & quantity) | Julien,Erendiro | 5hx2=10 | X | |
ID010 Improve leaflet | Julia,Alexander | 1hx2=2 | X | |
ID011 cardboard scale model | team | 2hx6=12 | X | |
ID012 Classes | team | 25hx6=150 | X | |
ID013 Structural Drawings | Julien,Alexander | 2hx2=4 | X | |
ID014 Dokuwiki References | team | 5hx6=30 | X | |
ID015 System Schematics | Erendiro | 3h | X | |
Writing Marketing, Ethics, Sustainability chapters | team | 24hx64=144 | X | |
Work capacity | 85 | |||
Velocity | 61 | |||
Sprint 4 - 28/03 to 03/04 | ||||
ID016 Communication Presentation | Alexander,Eren,Julien,Maïke | 4×1=4 | X | |
ID017 Eco efficiency chapter | Alexander,Ronald | 2×4=8 | X | |
ID020 Pitch Presentation | Alexander | 2 | X | |
ID024 Classes | team | 22×6=132 | X | |
ID021 Ethics | Julien,Maïke | 2×4=8 | X | |
ID018 Improve schematics and list of materials | Erendiro,Ronald | 2×5=10 | X | |
ID022 Marketing chapter | Julia | 4 | X | |
Work capacity | 103 | |||
Velocity | 22 | |||
Sprint 5 - 04/04 to 12/04 | ||||
ID 025 Project management part | team | 3×6=18 | X | |
ID018 Improve schematics and list of materials | Eren,Ronald | 5×2=10 | X | |
ID026 Classes | team | 28×6=168 | X | |
ID023 Interim Presentation | Julia | 4 | X | |
ID019 Interim Report review | team | 2×6=12 | X | |
Work capacity | 52 | |||
Velocity | 68 | |||
Sprint 6 - 22/04 to 30/04 | ||||
ID 022 Marketing | Julia, Alex | 4×2=8 | X | |
ID 027 Checking and changing format of pictures | Julia | 2 | X | |
ID 033 Building new circuit | Eren, Ronald | 2 | X | |
ID046 Classes | team | 6×6=36 | X | |
ID 028 Refrences | Ronald | 3 | X | |
ID 032 Final list of material | Julien, Eren,Ronald | 3×3=9 | X | |
ID 030 Checking spelling & grammar in the report | Maike | 4 | X | |
Work capacity | 210 | |||
Velocity | 36 | |||
Sprint 7 - 02/05 to 15/05 | ||||
ID041 Starting cultivation process | Ronald, Alex, Julien | 8×3=24 | X | |
ID036 Send e-mail to supervisors | Alex | - | X | |
ID 031 Research in cafeterias about buckets and coffe | Julien, Ronald | 1×2=2 | X | |
ID045 Classes | team | 4×6=24 | X | |
ID019 Interim Report review | team | 2×6=12 | X | |
ID 040 Business plan | team | 5×6=30 | X | |
ID 037 Planning | Julia | 1 | X | |
ID 029 Logbook | Maike | 1 | X | |
Work capacity | 176 | |||
Velocity | 38 | |||
Sprint 8 - 16/05 to 22/05 | ||||
ID 051 Collecting and preparing buckets | Ronald, Eren, Julia | 3×3=9 | X | |
ID 052 Collecting coffee | Ronald, Julien | 1×2=2 | X | |
ID 055 Cultivation/1st | Alex, Julien, Ronald | 6×3=18 | X | |
ID047 Classes | team | 7×6=42 | X | |
ID 043 Writing scientific paper, part 1 | team | 4×6=24 | X | |
ID 037 Planning | Julia | 1 | X | |
ID 029 Logbook | Maike | 1 | X | |
ID 042 Tracking cultivation process | Alex, Julien, Ronald | 2×3=6 | X | |
ID 038 Project developement, part 1 (conceptualisation) | Eren | 4 | X | |
ID 035 Checking and sending marketing plan | Julia, Alex | 1×2=2 | X | |
ID 034 Content for survey | Julien | 2 | X | |
ID 040 Business plan | team | 5×6=30 | X | |
ID 039 Talk with sponsors | team | 1×6=6 | X | |
Work capacity | 168 | |||
Velocity | 105 | |||
Sprint 9 - 23/05 to 29/05 | ||||
ID 057 Collecting coffee | Ronald | 1 | X | |
ID 056 Collecting and preparing buckets | Julia, Ronald, Eren | 3×3=9 | X | |
ID 054 Cultivation/2nd | team | 6×4=24 | X | |
ID 053 Tracking cultivation process | Julia, Alex, Ronald, Julien, Maike | 5×2=10 | X | |
ID 049 Writing scientific paper, part 2 | team | 4×6=24 | X | |
ID 048 Classes | team | 9×6=54 | X | |
ID 044 Sewing the chamber | Julien | 2 | X | |
ID 050 Project developement, part 2 | Eren | 5 | X | |
ID 029 Logbook | Maike | 1 | X | |
Work capacity | 156 | |||
Velocity | 74 | |||
Sprint 10 - 30/05 to 05/06 | ||||
ID 065 Making poster | Maike | 2 | X | |
ID 064 Cleaning contamination | Julia, Alex | 4×2=8 | X | |
ID 060 Cultivation/3rd | Julia, Alex, Julien, Maike | 5×4=20 | X | |
ID 053 Tracking cultivation process | Julia, Alex, Julien | 3×2=6 | X | |
ID 062 Putting paper together | Alex, Julien | 3×2=6 | X | |
ID 063 Classes | team | 7×6=42 | X | |
ID 059 Collecting and preparing buckets | Julia, Alex | 2×2=4 | X | |
ID 058 Collecting coffee | Julien, Maike | 1×2=2 | X | |
ID 066 Circuit improvements | Eren | 5 | X | |
ID 029 Logbook | Maike | 1 | X | |
Work capacity | 168 | |||
Velocity | 53 |
- Sprint Evaluations
The sprint retrospective is a meeting where a project team discusses what went well in a completed sprint and what could be improved. The team should also think of how to improve. The retrospective takes place after sprint review and before next sprint planning [33]. Our sprint retrospectives are shown in Table 11.
Sprints | Positive | Negative | Start doing | Keep doing | Stop doing |
---|---|---|---|---|---|
1 | Important work was done | Project planning was poor | Improve project planning | Focus on research | |
2 | Team has a better understanding of how to divide tasks and write them down in Planner, Brand logo and leaflet were created | Team was falling behind on writing wiki report | Provide teammates with an update of how task completion is going and ask for advice if needed | Writing report | |
3 | Wiki report was improved | Work was piling up and some tasks were moved to next sprint | Research on remaining report chapters | Writing remaining report chapters | |
4 | Ethics and Eco-efficiency chapters were completed in the report, Team had a meeting with potential sponsors | Project Planning chapter was not done | Project Planning chapter | Refining report | |
5 | Project Management chapter was completed, Interim presentation was prepared, Report was reviewed by the team members | Marketing chapter was not finished, List of Materials was incomplete | Practicing for the Interim presentation | Working on the report | |
6 | Interim presentation went well, Team received feedback on the report from the project coordinators | Report was not uploaded on time, Missing parts in report | Improving marketing chapter | Working on report | Talking about things not connected with project |
7 | We received the materials to grow mushrooms, New circuit was approved, The buckets were collected, Starting cultivation process | Some task were not completed | Motivating each other, Coming back on truck after student week | Cultivating mushrooms, Improving paper work | |
8 | Team started mushroom cultivation process, the Business plan was completed, Survey concerning mushroom consumption was put together | Writing remaining report chapters, Grow containers had too much humidity inside | Writing scientific paper | Check on mushroom cultivation process and record it | |
9 | Team started second cultivation process, Chamber for mushroom grow containers were built | Some buckets were contaminated | Putting scientific paper together, Send the survey | Check on mushroom cultivation process and record it | |
10 | Grow containers were moved to a new location, Third cultivation process was started | Contamination was spotted in all of the buckets | Try to get more people answering the survey | Check on mushroom cultivation process and record it |
- Conclusion
By properly defining project management has allowed the team to define a logical timescale for the project as well as addressing any potential risks and limits. It has determined an optimal management strategy in order to achieve all objectives. By defining sprints and through previous sprint analysis helps the team analyse their workflow and measure how well they work as a multidisciplinary team and adjust work ethics accordingly. Through risk analysis the team was able to analyse and overcome any potential setbacks. The team’s success will be determined by how well they can manage their time and how well they can stick to the optimal project management strategy.
The next chapter the team will begin to develop their marketing plan and defining potential marketing strategies based on market research.
- Marketing Plan
- Introduction
Marketing is a complex process, that is why there are many definitions of it. One of the most popular was defined by Philip Kotler, who is the main authority of modern marketing. Marketing is described by him as the process by which companies create value for customers and build strong customer relationship in order to capture value from customers in return [34]. In this chapter, it will be briefly described many activities such as marketing research, product development, distribution, pricing, advertising, personal selling, and others – designed to sense, serve, and satisfy consumer needs, while meeting the team’s goals.
- Market Analysis
A marketing analysis is a study of the dynamics of the market, in another words it's basically a business plan that presents information regarding the market in which the company is operating in [35], this section will focus on analysing those dynamics and establishing a positioning for the market.
Coffee Market
According to “Statista” the coffee market worldwide is worth over 79 billion euros in 2019 and has an expected annual growth of 4.8 % (CAGR 2019-2023) [36], being the European market worth over 31 billion € in 2019, with an expected annual growth of 3.1 % (CAGR 2019-2023) [37], and furthermore revenue in coffee segment amounts to 1,899 million € in 2019 in Portugal with an expected annual growth of 2.3 % (CAGR 2019-2023) [38].
1000 kg of fresh berry gives about 400 kg of wet waste pulp [39]. Portugal has an annual coffee consumption of about 40 tons of coffee which accounts for 16 tons of coffee waste every year [40].
Portugal is the third country that pays the most for coffee [41].
So, as can be seen, there's a really big market opportunity to deal with all the coffee waste that is thrown away.
Mushroom Market
The worldwide mushroom market was evaluated in about 35 billion USD according to “FreshPlaza” in a recent study dated to 2015, between 2016 and 2021 is expected an overall growth on the market of about 9.2 % [42]. Some sources even state that the market is expected to be worth 50 billion by the end of 2019 [43].
The biggest growth is expected in the Asian countries. Mushroom consumption in China, Japan and India are quite large. Partly because of the growing focus on healthy and organic foods, demand in these countries will continue to grow. Europe is the largest market for cultivated mushrooms, accounting for more than 35% of the global market. Moreover, demand is on the rise in North America, and South America is also recording explosive growth. Meanwhile, Africa and the Middle East recorded a reasonable growth [44].
The main species of mushrooms consumed in Portugal are white mushroom (Agaricus bisporus), brown mushroom (agaricus subrufescens), shiitake (Lentinula edodes), black mushroom from Japan (Hypsizygus tessellatus), and wild mushrooms [45].
The domestic market is made mostly through hypermarkets, supply markets, hotels and restaurants. According to data from the GPP (Planning, Policy and General Administration Office), about half of the production is disposed of outside the country, namely for the Spanish and French markets [46].
Through an inquiry made by [47] it was possible to conclude that one of the major obstacles in the commercialization of mushrooms is the establishment of distribution channels, followed by the difficulty of financing and thirdly the culinary culture [48].
Sustainable foods market
Growth in Healthy Eating in Europe. Across all four types of wellness food, shoppers are buying more now compared to 2-3 years ago, healthy food has increased by 41 %, organic by a third (34 %) and vegetarian and free-from foods by a quarter (26 % and 24 % respectively).
What’s more interesting though is that this sector still has far to go. When asked in the next six months whether they intended to spend more, just under a fifth were going to increase their spending across the four different categories [49].
Growth in Healthy Eating in Portugal As shown in a study conducted by the Center for Applied Studies of Catholic-Lisbon, School of Business & Economics in partnership with ANIPLA regarding Portuguese dietary habits 65 % of respondents prefer to consume only organic foods [50]. To further support this growth, the Portuguese Association of Distribution Companies (APED) confirms that “the category of organic products is in full development” and cites the “Target Group Index” study, published in 2018 by Marktest, according to which 47,7 % of Portuguese buy organic products [51], and this growth has been followed by a strong commitment by most of the big supermarkets in their own biological array of products, making them no longer a niche market, occupying more and more space on the shelves, and at more affordable prices. Pingo Doce, which already commercialized organic fresh products, recently launched a new brand of its own, “Go Bio”, with processed products, joining Aldi, Continente, El Corte Inglés, E. Leclerc, Intermarché, Jumbo and Lidl [52].
Competition
Before starting a business it is important to understand the market you are entering by analysing its strengths and weaknesses to determine the attractiveness and profitability of the potential market. Porter's Five Forces model acts as a framework for analysing a company’s competitive environment. Porter's Five Forces is a model that identifies and analyses five competitive forces that shape every industry and helps to determine these strengths and weaknesses. The number and power of a company’s competitive rivals, potential new market entrants, suppliers, customers and substitute products influence a company’s profitability [53]. Analysing these elements can be used to guide business strategy to increase competitive advantage.

Competition in the industry
This Force refers to the number of competitors and their ability to undercut a company. The more competitors along with the number of equivalent products/services they offer the less power a company has in the market. Competition can drive prices down, similarly, if rivalry is low then company has more power to charge higher prices. Competition drives innovation to remain competitive in the market [55]. Mushroom farming is nothing new and already has many competitors and therefore the team must focus on its unique selling point and make product's benefits clear to the customer. The business must differentiate itself from other mushroom farms by acting more as a supplier of resources and information rather than acting solely as a mushroom farm. By doing this the company can develop a much richer customer business relationship ensuring long term and returning customers. The customers will buy into the service rather than just a product. If competition is too similar then it reduces the profit potential of the business.
Potential of New Entrants into an industry
A business’s power is also affected by the force of new entrants into its market. The less time and money it costs for a competitor to enter a competitors market and be an effective competitor, the more a companies position can be significantly weakened [56]. The team must take this into consideration as what makes a mushroom business so attractive is that there is no need for massive capital investment, especially because much of the cultivation process can be done with waste from other industries. However, if the team focuses on spreading awareness about sustainable food system and work as a provider of information and resources, it will not be in direct competition with mushroom producers. The business will be based around selling the mushroom cultivation kit but by providing a service that surrounds the product it will provide multiple income streams. The aim is also to secure some funding for other organisations who want to be part of the mission in spreading awareness to encourage a change in a more environmentally conscious direction. Having multiple income streams ensures more profit potential for the business to succeed.
Power of Suppliers
This force addresses how easily suppliers can drive up the costs of inputs. It is affected by the number of suppliers; how unique these inputs are and how much it costs to switch from one supplier to another [57]. This is where the team has quite a good advantage. Because the team wants to adopt a circular economy approach there are very few inputs which are controlled by suppliers. The business is based around the idea of reusing waste. Mushrooms will be cultivated using coffee waste and straw. Both are other industries waste so it is not only free but also available in abundance. Once the business has established itself in the market with a positive image the team may even be able to charge cafes to pay small amounts to collect their waste as it promotes their business as supporters of a sustainable solution. Even the mushroom spawn can be recycled over and over once it has entered the system. This allows the business to operate without any fluctuation in supplies.
Power of Customers
This refers to the ability of customers to drive prices down. It is affected by the number of customers the business has, how significant each customer is and how much it would cost to new customers or markets. A company that has many smaller independent customers has much easier time charging higher prices than it would be having a smaller client base [58]. The more power the customer has the more they are able to negotiate. Because the team's business is focusing on local markets rather than a global market, the customer base may not be that big. However, the team wants to focus on building loyal customers and building a strong business customer relationship base, which is fair to both parties. By building this sense of community rather than strictly business, customers will be more willing to buy into the business. Loyal customers ensure long-term profit.
Threat of Substitutes
Substitute goods and services that can be used in place of a company’s products or services pose a potential threat. Companies that produce goods or services for which there are no close substitutes will have more power to increase prices [59]. The team has tried to differentiate itself from other potential competitors to create a unique service. There may be a risk of substitutes outside mushroom cultivation, however, these are not direct competitors. As the business grows and develops with customers needs and wants the business could branch out into home cultivation kits outside of mushrooms.
Understanding all these five forces and how they can be applied to an industry can enable a business to adjust business strategy to better use its resources to generate higher earnings.
Survey Results/Analysis (Primary Research)
The first section of the survey was dedicated to understanding the profile of the participants and their eating habits. Questions included age, sex, occupation, household size and food preference. The second half was focused more on people attitude towards sustainable food, mushrooms and the last section was to gauge people interest in our product itself and the price of the product. The full results can be found in the deliverables section.
The survey was posted through different portuguese facebook groups ( 2 vegetarian pages, 1 student page ), general publications as well as messages directed to portuguese peoples.
In total, we received 102 responses which are enough to draw reasonable conclusions. Most people who responded were between the ages of 18 and 24 (55.9 %). We had responses from both male (59.8 %) and female (40.2 %) participants. There was a large variety of occupations however the majority were students. 33.3 % of the Participants said they were vegetarian and 26 % were omnivores. Ideally, the team would have liked more responses with a larger variety of people (age/occupation) to make it easier to generalise results and make valid conclusions.
In the second half of the survey participants were asked how if they agree with the following statements: We need to reduce our carbon footprint, we need to reuse and recycle more, we need to eat less meat and lastly if we should try to buy local products. The large majority of participants strongly agreed with the statements with only a few exceptions. This shows that people are environmentally conscious and are aware of what action needs to take place. This shows that people are aware of the environmental issue we face today and will eventually seek for businesses and products that support these statements. If the team can market and promote the product as something that addresses these environmental issues, consumers will see much more value in buying a product like this. 49 % of participants eat mushrooms twice and week and 41.2 % eat mushrooms 3 to 4 times a week. When asked what they look for when buying mushrooms 65 % of participants said quality was most important followed by price (50 %), followed by origin. Majority of people said they eat mushrooms with their main plate, not as their main plate and the reason for eating mushrooms was because they are delicious (44.4 %) and healthy (36.4 %). 22 % of participants said the reason they eat mushrooms is because they are considered sustainable food. This information is of great value to the team as it acts as a marketing guideline and shows what consumers are looking for when they buy mushrooms. If the grow kits can guarantee quality mushrooms with a weekly yield that can be cultivated at home, then the products addresses all the needs consumers looks for when buying mushrooms. It is important that the product is marketed not only as a sustainable product but also as a rewarding process which provides quality, healthy and delicious food. This in conjunction with an educational aspect makes the entire process much more fulfilling and justifies buying a grow kit instead of just buying mushrooms from the supermarket.
Lastly, we asked participants how interested they were in the product the team was developing and asked them how much they would pay for it. Regarding the bucket grow kit, people showed quite high levels of interest and the average estimated price was set to about 10-15 euros. This shows that there is a want for the team’s products. The price estimated at 10-15 euros is more than reasonable and team can sell at this price while remaining competitive and profitable. Interest for fruiting and monitoring/control chamber was not as high and participants estimated the cost between 10-20 euros. All the components needed to make the chamber cost 98 euros. This price is much higher than what participants said they would pay for it. This indicates that people do not think the function justifies the price. This may be because they have not understood the whole process and are not aware of the benefits this control system brings. For this reason, the fruiting and monitoring/control chamber will be marketed more at people with a much higher understanding and interest in the whole process. The ‘mushroom freaks’ so to speak. Once customers go through the entire process a few times they may develop more of an interest and a need for the chamber. The team have also considered using a deposit system where the consumer pays a deposit for the chamber and then pays a monthly rental fee instead of buying the whole thing. This allows the business to slowly pay off the price of the chamber. This creates a much smaller initial investment and allows consumers interest to grow with the product.
- SWOT Analysis
SWOT analysis stands for: strengths, weaknesses, opportunities and threats. The purpose of this extremely useful framework is identifying and analysing the internal and external factors that can have an impact on the viability of a project, product, place or person. A SWOT analysis is often used as a strategic planning exercise at the very beginning of the project. The framework is considered as a powerful support for decision-making because it enables an entity to uncover opportunities for success that were previously unarticulated or to highlight threats before they become overly burdensome [60].
SWOT analysis is presented in the Figure 9:

- Strategic Objectives
Strategic objectives are the steps and accomplishments, which are established by an organisation in order to realise the ultimate goal. Objectives help across the team to understand the goals and to determine whether the strategy is effective and the tactics are being well executed. While setting the objectives it is important to specify measurable outcomes that will be achieved within a particular time frame [61]. To state them it is used the SMART criteria approach, which has several different variations, which can be used to provide a more comprehensive definition of goal setting [62]:
Letter | Variations |
---|---|
S | specific, significant, stretching |
M | measurable, meaningful, motivational |
A | agreed upon, attainable, achievable, acceptable, action-oriented |
R | realistic, relevant, reasonable, rewarding, results-oriented |
T | time-based, time-bound, timely, tangible, trackable |

General mission and vision strategic objectives:
Economical strategic objectives
- Develop a Business based around mushroom cultivation which is both profitable and economically sustainable.
- Maintain growth for the first 5 years of operation.
Customer/Learning strategic objectives
- Introduce an innovative solution into an existing market.
- Build customer database by introducing a high-quality product and service.
- Provide high-quality training and workshops for customers. To encourage customers to live in a more sustainable way.
- To continuously learn and adopt current best practices.
Environmental Strategic objectives
- To adopt a circular approach to waste.
- To adapt processes to be efficient as possible to reduce carbon footprint.
- To continually adapt to best environmental practices.
- To spread awareness to encourage more environmentally friendly practices.
Measurable and time-framed objectives in terms of mushroom project farm:
- Conduct the potential customer survey till 15-05-2019
- Finish testing phase till 24-05-2019;
- Create a website and social media accounts till 31-05-2019
- Generate more than 150 likes and 50 comments on our website and social media before 14-06-2019
- Build a working prototype before 10-06-2019;
- Finish the project report before 14-06-2019;
- Segmentation
The team must decide to exactly what market they are going to target. Despite the Global production of mushrooms increasing and an increase in global imports and exports of mushrooms [64] the team must decide what segment they want to focus their efforts on. Since the whole idea of the business is to bring food with low carbon footprint to consumers the team wants to focus on local markets. The team must decide exactly where they fit in along with all potential competitors. To do this they must establish segments in the market that they should focus in order to product segment specific marketing strategies. The segmentation is split into geographic, demographic, behavioural and psychological.
Geographic
World mushroom production in continuously increasing from 0.30 to 3.41 million tons roughly over the last 50 years from 1961 to 2010 (Figure 11). Also export and import trend lines show that mushroom exports/imports have continuously increased over the last 40 years (Figure 12). Trade of mushrooms in the European Union is significant and is reflected in table. The European Union mushroom production was about 27 % of the total world's production in 2010. Netherlands is the largest producer and consumer; Poland is the largest exporter and UK is the biggest importer. France and Spain are also large producers and consumers [65]. There is not a lot of information for Portugal which may indicate the mushroom market in Portugal may not be very big. This may be due to poor marketing and may be lacking thought and investment. Therefore, it is important to consider the marketing for success in Portugal. Fresh mushrooms have a very short shelf life, cannot be transported long distances without refrigeration and since the whole idea of the business is to bring low carbon food to consumers the team wants to focus marketing plan directly the local markets in Portugal.



Demographics
- Gender: Male & Female
- Age: 21-55
- Income: Average
- Family situation: Individuals and Families
- Interest: Healthy food, Organics and environmentally friendly.
Regarding age basing on the survey [69] as respondents were older, they were more likely to eat fresh mushrooms therefore the team wants to have a large age range to spread awareness. According to a survey [70], women were more likely to consume fresh mushrooms with higher frequency, but there is no need to create a target group based on gender when selling the product which is dedicated for everyone. The initial plan is to divide the sales into three levels basing on the interest, in order to make it affordable for everyone. The product will be aimed at families as this targets both a young and older consumers and is most effective in spreading awareness.
Behavioral
Not only a one-off purchase of a mushroom farm, but a simple food production system designed to bring fresh low carbon mushrooms to your plate. The system is designed to appeal to a range of people due to its autonomous nature which allows different levels of involvement in the cultivation process. Cultivation of mushrooms does not require lots of space so this mushroom food system is perfect for city dwellers who do not have access to large growing spaces. Development of a customer loyalty relationship where the business will offer substantive support and provide all the necessary resources and education alongside the process. Education is aimed in spreading awareness about sustainable foods and promoting a healthy diet.
Psychographic
Psychographic target will be aimed at open minded individuals which are concerned with sustainability and are environmentally conscious. The potential customer should have some interest in the cultivation process and growing organic foods. However not much knowledge is required as product is supported with all information needed. The motive of the potential customer should be to encourage sustainable food production which naturally stimulates a healthy diet by having access to fresh and organic produce. The system has been automated to accommodate different lifestyles and levels of interest.
- Strategy/Positioning/Brand
4.6.1 Positioning Statement
For all mushroom lovers who want a high quality fresh and locally grown product, Waste to Fungi is the sustainable grey oyster mushroom farm that delivers the kit, which gives the possibility to grow easily ecologically from coffee waste delicious, tasty grey oyster mushrooms, unlike traditional grow kits and mushroom farms, Waste to Fungi offers the product which is simple, easy to use, supports local economy and it is eco-friendly oriented by minimizing CO2 emissions caused by logistics and what is more, transforms waste into nutritious food.
4.6.2 Benefit
The concern on product benefit should be not only living life green but also the nutrition and health aspects of eating mushrooms. According to Health Benefits [71], Grey oyster mushrooms are very healthy and nutritious. A cup of raw grey oyster mushrooms provides around 28 calories and 0.35 grams of fat, 2.85 grams of protein and 2 grams of fiber. The same amount also provides 361 mg of potassium, 0.095 grams of Vitamin B6 and 33 μg of Folate. Grey oyster mushrooms are loaded with nutrients and vitamins which make them ideal for a healthy diet. They are free from fat, cholesterol, gluten, low in calories and sodium. They have high amounts of iron compared to meats.
4.6.3 Marketing campaign
Broad goals: Promote Waste to Fungi grow kit and service Increase brand awareness
Main goal: Sell 500 of buckets in first 3 months of operation
Sub-goals:
- Hold 12 workshops in 3 months of operation
- Get at least 5 people attending each event
- Get 600 likes to Waste to Fungi facebook page
- Get 1000 for Waste to Fungi instagram profile
- Get 2000 amount of views for promotional video on youtube and instagram
After 3 months of operation, the team will see if the set goals were achieved. Analysis will be conducted based on the results and new measurable goals will be set.
How to reach out to our potential customers:
The team has agreed that the most effective way to spread awareness around Porto and the north of Portugal is to have a Promotion Representatives. The team has chosen 4 organisations in Porto that could be great representatives. The four organisations are: Espaco Compasso, Casa da Horta, Casa Bo and Ananda Forest. All of these are multicultural associations that seeks to facilitate living and sharing of holistic knowledge, according to permaculture premises. Their vision is to generate local actions in Ecology, Politics, Economy, Education and Art, that are being applied in the functioning of the association. Space has become a platform for events, classes, workshops and debates, and an atmosphere of exchange of ideas where any member can propose a project, and anyone can become associated. All these associations are a great place to advertise and host initial workshops as they already have a strong customer base which fit perfectly the profile of people ‘Waste to Fungi’ will try target. Posters and leaflets can be distributed amongst the organisations and can also be distributed around the universities. Poster and leaflet will have links to the businesses Facebook and Instagram page where they can find out more information. The Business could also host open days, only available for students, who would like to volunteer in exchange for an enriching learning experience. This would also be a great way to spread awareness. One of the initial marketing strategies are to host workshops inside these organisations. They already have a space where workshops can be held. Workshops are a great way to get new customers and get them excited about the business. Workshops will last half a day. Attendees will learn all about circular economies and mushroom cultivation in the first half of the workshop. Lunch can be provided which used mushrooms cultivated by ‘Waste to Fungi’. The second half of the workshop can be dedicated to building their own bucket. This is a great way to get people talking about the new business and a great way for Waste to Fungi to talk to potential customers.
Platforms through which we advertise:
Waste to fungi will create a website, which would include information about company’s service and concept, as well as all the information needed regarding events and workshops. Website will have a e-shop, where grow kits can be purchased. To keep people interested and up to date with company’s activities and news, facebook and instagram pages would be created.
- Adapted Marketing-Mix
Marketing mix is a framework for the tactical management of the customer relationship, including (the 4-Ps):
- Product
- Price
- Place
- Promotion
4P model is presented in Figure 14 and subsription types of product in the Figure 15:


- Pricing
To make the pricing of their buckets, the team decided to estimate its costs. The costs were divided in two categories, the fixed rates and production rates.
The fixed rates presented in Table 13 depicts the labor, shop rent, bills, and material investment that would be needed to have an auto running business.
Description | Quantity | Monthly rate [€] |
---|---|---|
Labor | ||
Worker running the production and advertising | 1 | 750 |
Shop and production site | ||
A 30 sqm shop were production would be held near boavista | 1 | 400 |
Electricity and water | 1 | 100 |
6000€ invested into material for production over 24 months | 1 | 250 |
Total : | 1500 |
The production rates presented in Table 14 depicts the different costs needed to provide raw material. It is considered that enough buckets are within the system and a consign would be paid by customers, this cost is henceforth not taken in count. The coffee would be collected in partner coffee shops and restaurants by bikers paid at a rate of 7 € per hour and collecting an average of 10 kg of coffee per hour. The mycelium would be provided by Horta do Marão. Considering a mix including 90% of coffee and 10% of Grey Oyster spawn, the raw material would cost 0,93 € per kg.
Description | Rate [€] | Quantity | Unit |
---|---|---|---|
Coffee | 7 | 10 | kg |
Grey Oyster Mushroom mycelium | 20 | 6 | kg |
Average rate : | 0.93 | 1 | kg |
In order to know how many units the team needs to sell to be profitable, they did the following table with different selling plan. To be profitable they need to sell more than the quantities displayed in Table 15. This pricing and these sell objectives seem highly possible considering the survey and the expected trends depicted in the marketing chapter.
Description | Average cost [€ per unit] | Average Selling Price [€ per unit] | benefit [%] | Number of units to compensate costs |
---|---|---|---|---|
Small bucket ( 1 kg ) | 0.93 | 8 | 88 | 213 |
Medium bucket ( 3 kg ) | 2.79 | 15 | 81 | 123 |
Large bucket ( 5 kg ) | 4.65 | 20 | 77 | 98 |
Combinated plan | ||||
40% of S, 40% of M, 20% of L | 2.418 | 13.2 | 81 | 56S, 56M, 28L (140) |
20% of S, 60% of M, 20% of L | 2.79 | 14.6 | 81 | 26S, 76M, 26L (128) |
20% of S, 40% of M, 40% of L | 3.162 | 15.6 | 80 | 24S, 48M, 48L (120+) |
- Budget
Initial spending will be on printing posters that will be distributed among promotion representatives, universities and put up in food markets. 100 posters would be sufficient. The team was able to get a quote from ‘Grafipronto’, a printing service in Porto. The price per unit for 100 A3 colored Posters was quoted at 22 € (price per unit is 0.22 €).
The team has also calculated that is would cost 50 € to run a workshop for 5 attendees. Workshop would run for 3 hours plus 1 hour of prep time. Teacher running the workshop will be paid 5 € an hour (4h x 5 € = 20 €). Cost of Substrate per person 4.5 € per person. This includes transport cost for coffee and price of Mushroom spawn. Lunch will be provided with mushrooms incorporated into the dish. Lunch will cost 3 € per person (3p x 5 € = 15 €). This brings to total cost for running a workshop for 5 people to 57.5 €. Tickets will be sold at 20 € per person. So if 5 people attend money returned will be 100 €. 15% commission must be given for the rent of the workshop space. Therefore ‘waste to Fungi’ make a profit of 17.5 € per workshop. This may not seem like a lot however the initial objective for workshops is not make money but to advertise and establish new customers.
The budget for the promotional video has been set at 350 €. The team looked into hiring an independent film maker which would cost 200 € plus another 150 € for renting the equipment.
The budget breakdown is presented in Table 16.
Description | Price [€] |
---|---|
Posters | 22 |
Workshops | 57 (39.5) |
Film maker | 200 |
Equipment rental | 150 |
Total: | 429 (411.5) |
- Strategy Control
To ensure the team and business is operating at full potential a plan-do-check-act cycle can be integrated to ensure constant improvement and to prevent reoccurring mistakes. This is an essential part of lean manufacturing/management and encourages constant improvements in the process and service [72].

When should you use PDCA cycle?
- Starting a new improvement project
- Developing a new or improved design of a process, product or service
- Defining a repetitive work process
- Planning data collection and analysis in order to verify and prioritise problems or root causes
- Implementing any change
- Working towards continuous improvement
The Procedure
- Plan: Recognise opportunity and improvement potentials and define objectives and processes for desired result.
- Do: Test the potential solution. Carry out a small-scale study first.
- Check: Review the test, analyse the results and identify what you have learned and whether or not the potential solution is viable.
- Act: Act based on what you learned in the study step. If the change has not worked, go through the cycle again with a different strategy. If potential solution is successful, incorporate what you have learned from the test into wider changes. Use what you have learned to plan new improvements, beginning the cycle again.
This tool is very important in ensuring a high-quality product and service. It allows the process to be adapted based on customer and market requirements. It also serves as a tool to check whether not the marketing plan has been effective and if it needs to be readjusted to better attract the intended target group.
- Conclusion
Based on this market/economic analysis, the team has decided to create a service whereby waste coffee is collected and transformed into grow kits. Growkits will then be sold to consumers, which can be purchased on site at the teams production site.The business intends to generate profit by offering 3 sizes of growkits (1lL, 3L and 5L) for different levels of interest. Growkits will be made and incubated on site. Once the mycelium has fully colonised, they can then be sold to consumers, where they can grow fresh mushrooms at home. Any excess growkits which are not sold, to avoid wasting them, they will be used directly by 'Waste to Fungi' to grow fresh oyster mushrooms which can then be sold on the local market. Buckets will be promoted as healthy, sustainable and educational and will be targeted to people who are trying to be more environmentally conscious and want to grow food at home.
Waste to Fungi would also like to offer customers a subscription pack where they pay a monthly fee in exchange for discounts on all the products and workshops. They will also have access to information and resources.Information available will include full instruction on cultivation process including tips and tricks, nutritional value of specific mushroom, recipes, information on other sustainable food systems and access to a cultivation forum. All of this will be integrated into an app.The business also intends to make profit by creating workshops about cultivating mushrooms and other sustainable food systems. Once the business is established and recognized in the local community, a small fee can be charged for coffee waste collection in return they can advertise themselves as a supporter to a sustainable solution.
The next chapter introduces briefly the Eco-efficiency Measures for Sustainability of a mushroom farm.
- Eco-efficiency Measures for Sustainability
In this Chapter the team will be addressing any sustainable concerns by looking at the Eco-efficiency of not only the cultivation process but the business in its entirety. The team will not only look into the environmental sustainability but will also consider social and economical side as well as doing an life cycle analysis (LCA) of the concept in mind.
- Introduction
With more and more pressure on businesses to be sustainable, advances in environmental management have improved drastically over the last years. However, with environmental concerns becoming more obvious, businesses today need to take greater action and responsibility to ensure a healthy and sustainable future. Businesses usually focus their efforts in environmental control on the end of the product life cycle which actually don’t produce environmental solutions, but rather prolong the problem. More environmentally conscious businesses are implementing other sustainable concepts and practices that have a more significant impact on the environment, emphasising the principles of maximum value with minimum resources. These concepts and practices include optimising eco-efficiency, extending product responsibility and function, design for the environment, design product services and by-product synergy (one industry's waste stream is another industry’s primary resource). Many of these concepts are derived from a more circular economy business model. This model aims to transform traditional linear models of production, whereby raw materials enter and products and its waste exit the system into a more integrated (circular) industrial ecosystem. This model uses optimisation of energy and material consumption and waste minimisation, where the non-valuable outputs of one process (commonly denominated ‘residual waste’) serve as valuable input for other processes [74]. Businesses must analyse their product life cycle and decide what areas are best suited to implement potential solutions and optimise as much as possible. Businesses need to go above and beyond environmental regulations in order to reduce the environmental impact of their product and services rather than not making it worse. Each stage in the product life cycle must share this responsibility and implement potential solutions as best as possible. In order for these efforts to be successful, the economic and regulatory systems surrounding the development of the business must be considered to better support potential solutions and encourage better environmental practices.
- Environmental
Waste to Fungi pursues the idea of being sustainable as a business. It means adopting a more circular approach by which materials are reused that would be otherwise thrown away. Coffee leftovers are used as a substrate for a mushroom to grow on. This means the service uses by-product synergy as waste from another industry is used as another primary resource. Grow kits will use plastic buckets from various food industries, thereby extending the life cycle of the buckets. The growing process will be carried out in the same containers. Waste resource collection and product distribution will all be conducted locally to minimise the negative impacts. It means less pollution created by transportation. Electrical components and mushroom spawn may have to be sourced externally; however, efforts will be made to source as local as possible. This not only reduces emissions but also supports a more local economy. Process of mixing substrate with mycelium does not require energy as it can be done by the human hand. Grey oyster mushrooms are going to be grown domestically, which means the gap between the consumers' plate and production point is shortened, thereby reducing the foods' carbon footprint. After the growing process has been completed, buckets are returned to the company for a new cycle, promoting a more circular economy. Buckets have a monitoring system (as an option), which allows the consumer to maximise outputs without increasing inputs. The system is modular, which allows defective components to be easily replaced, rather than replacing the entire system. A full life cycle assessment could be conducted in order to point out areas of weakness in the business, that can be optimised to make it as sustainable as possible. This will be done further into the chapter.
- Economical
Economic sustainability are strategies for making the most out of available resources, to their best advantage. The idea is to promote the use of these resources in a way that is both efficient, responsible and likely to provide a long-term environment and economic benefits, while returning a profit. The concept uses coffee waste and plastic buckets from another industry providing a suitable substrate and growing container for no cost. The deposit system is implemented into the business, which uses concepts of a circular economy to not only produce less waste but to also reduce costs. It maximises the reuse of materials. It may reduce profits, but also reduces waste. The company adapts the return policy to be as sustainable as possible, but must make sure it generates enough profit to maintain the business.
- Social
With the concept of sustainability, people mostly think of the environmental and economic side of it. But more attention is now being put on the idea of social sustainability, where by before was neglected. Social sustainability refers to the well being of all. By definition, it is the ability of a community to develop processes and structures which not only meet the needs of its current members but also support the ability of future generations to maintain a healthy community [75]. Industries are recognising that social justice and social rights are an integral part of sustainability. It is truly an international effort, as the groups creating the international set of social standards for all members are called the Fair Trade Labeling Organization International. They are researching aspects of labor welfare and rights, making recommendations, and hoping soon to implement new standards through developing guiding documents [76]. The goal as a company is to provide people with access to fresh, healthy and organic food which in terms adds to their quality of life. Surrounding the business there is an educational aspect by which the service hopes to provide information and courses that teach people and families about the process and benefits of growing mushrooms at home. This is not only an enriching and rewarding process but expands people awareness and knowledge in sustainable food systems as well as providing food security. The company will also encourage the fair trade of local resources to stimulate the development of sustainable communities.
- Life Cycle Analysis
Life cycle assessment:
The life cycle assessment of a product (LCA) is a great tool to calculate the environmental emissions at each point during the life cycle of the specific product or industry, starting from extraction, manufacturing, use and distribution all the way to disposal [77]. It looks at a product from cradle to grave. As people demand more sustainable foods this tool becomes more necessary to consumers as this information can effect their purchasing decisions. The objective in this section is to analyse the environmental impacts of waste within the coffee production and see if there are any week areas within the cultivation process which can be optimised to be made more environmentally friendly.
Raw material extraction
In order to cultivate the mushrooms, a substrate for the mycelium to colonise on is needed. In this case, the coffee waste is being used. By using another industries waste as one of the main resources in the production of the mushrooms is a big sustainable advantage. It not only gives value to waste which would otherwise be thrown away, but also uses more of the coffee grounds potential by using the remaining 99% of the nutrients still in the coffee grounds after extraction to grow mushrooms. Another big advantage is that by providing a service of waste management for the coffee waste makes the resource free, making it more economically sustainable. Other resources such as plastic using in the production process need to be taken into account too; however, if the business is able to repurpose, even recycle buckets as grow containers instead of using single-use grow bags. Then again, the business is adding value to recycled material and extending the life of the buckets too.
Production process/Use of Product
The actual production of the mushrooms has almost no negative effect on the environment. Despite the small control unit for the grow chamber which requires small amounts of power to use, the process requires very little resources. Small amounts of light and water to optimise the conditions of the grow chamber but this is all.
Post Harvest
Once the mushrooms have been harvested the coffee waste will no longer have any nutrients left in it. This can now be used into compost and other growing mediums for plants. The grow buckets can be reused over and over to a certain point, therefore, extending the life cycle of it. Sterilisation of the bucket is required, but can be done with rubbing alcohol which does not require high amounts of energy nor does it have any negative effects on the environment, if used appropriately. By introducing a deposit system for the buckets and the growing chamber it encourages as much reuse as possible.
The whole cultivation process all the way from resource extraction to post-harvest tries to adopt a more circular approach by which resources are fed back into the process to maximise their use and extend the life as much as possible and by not using any single-use plastics. Because production is done at home it also heavily reduces the foods carbon footprint as it does not have to travel to reach the customers plate.
- Conclusion
As people become more aware of sustainability practices, businesses will try to adopt a more circular economy approach. Whereby waste is filtered back into production, therefore, less extracted resource is used in a production process. Products are made of reused materials. When a lifetime of a product is exceeded, materials and parts are recycled. Waste to Fungi aims to be sustainable through reusing coffee waste and plastic buckets, this adds value to another industries waste and so their life is extended. There is the added benefit that these materials are free and will not generate much costs for the business. Furthermore, energy consumption is minimized by avoiding sterilization process as coffee is already sterilized through the brewing process. In addition to that, process of mixing substrate and mushroom spawn can be done by human hand, again saving energy. The circular economy concept will be achieved by establishing a cycle for the product. Once the customer has harvested mushrooms from the grow kit, it is returned, cleaned and reused as a growing container. A small low-power monitoring system is added to the grow kit making it easier for the customer to track the humidity and temperature levels to maximize yields and efficiency of the kits. Process of growing mushrooms at home is educational as well as rewarding, providing fresh, healthy and tasty food. This not only promotes a healthy diet but also promotes good environmental practices. The business aims to be sustainable not only through its practices and techniques but by spreading awareness and promoting sustainability by connecting people back to healthy, organic and low carbon food.
- Ethical and Deontological Concerns
- Introduction
Ethics regarding business is not simply about regulatory compliance and legal protection. When talking about ethics, it includes a commitment to quality products, attentive customer service, and taking care of employees and the local community. As a company, it is very important to take care of ethical concerns as it shapes its image and market position as well as it contributes to its trustworthiness. It ensures stable development and should, therefore, be the basis for the functioning.
As ethical behavior is of utmost importance while designing a new product, this chapter will cover all different aspects such as Engineering, Environmental and Sales and Marketing Ethics. In Figure 17 the most important ethical values are represented.
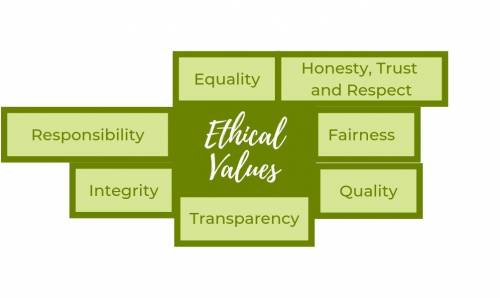
- Engineering Ethics
Engineers through their position in the industry, and the creation and development of new products have a really important role, it is therefore really important for those professionals to behave in a good ethical and moral way.
Indeed, engineers play a major role in today’s society, through three main different ways:
Human: Engineers should be developing and creating products in accordance with safety, health and welfare of the public.
Environment: Engineers should be developing and creating products that are not, or as less harmful as possible to the environment. By studying the life cycle of the product in order to achieve it. This is one of the biggest challenges of this century as our society has to face climate change.
Society: Engineers should be developing and creating products for the benefits of whole and contributing for a better society, by creating solutions to connect, or help people in a more general way.
Code of ethics was discussed in many engineering societies. The one that was the more up to date is the Code of Ethics brought by the National Society of Professional Engineers [78].
Their Code of Ethics is composed of three main things:
Fundamental canons, rules of practice, and professional obligations.
The fundamental canons being the following:
- Hold paramount the safety, health, and welfare of the public.
- Perform services only in areas of their competence.
- Issue public statements only in an objective and truthful manner.
- Act for each employer or client as faithful agents or trustees.
- Avoid deceptive acts.
- Conduct themselves honorably, responsibly, ethically, and lawfully so as to enhance the honor, reputation, and usefulness of the profession.
- Sales and Marketing Ethics
When thinking about advertising a product, doing it ethically is less of a marketing strategy and more of a philosophy which should seek to promote fairness, honesty, and responsibility. Ethics is always a difficult subject because everyone has slightly different ideas about what is right and what is wrong. Therefore, ethical marketing is not a strict list of rules to follow, but a general set of principles which should support companies as they decide on their marketing strategies. In fact, there are 8 different principles to be aware of:
- The common standard of truth will be observed in all forms of marketing communication.
- Personal ethics will guide the actions of marketing professionals.
- Advertising is set apart from entertainment and news and the line is clear.
- Marketers will be transparent about who is paid to endorse their products.
- Consumers will be treated fairly, depending on who the consumer is and what the product is.
- Consumer privacy will be respected and upheld at all times.
- Marketers will comply with standards and regulations set by professional organisations and the government
- Ethics should be discussed in all marketing decisions in an open and honest way [79]
Also, since unethical advertising is not necessary against the law and is just as effective as ethical marketing, many companies use it for their advantage. Taking that into account, it is of high importance for Waste To Fungi to treat their customers fair and advertise the service and product in the most transparent and honest way possible. That is to ensure reliable and trustworthy reputation.
- Environmental Ethics
As the world population increased sevenfold from 1 billion up to over 7 billion inhabitants [80] during the past two centuries, so did the consumption of the planet natural resources. This behaviour puts major stress on the life-supporting capacities of the planet. As a result, humans became responsible for several environmental issues such as global warming and climate change as they forget about the value and the moral status of the environment and started to exploit the planet and non-human creatures for their own advantage and comfort. The main core of environmental ethics is finding the balance between social, economic and environmental aspects and try to be more sustainable in all actions [81].
When designing mushroom grow kit, Waste to Fungi is conscious about the impact on the environment – and this should be kept as low as possible. As the service strives to be a completely circular one, taking back Grow-Kits which do not grow mushrooms anymore and reusing the chamber as well as using coffee grounds as the main component of the product which would otherwise be thrown away, the company is making an effort on being as sustainable as it can be. Waste To Fungi does not want to contribute to the pollution of the planet and produce more waste. Also, because people will be able to grow their mushrooms at home the company will decrease CO2-emissions to a minimum as mushrooms won’t need to travel long to finally arrive at the end-consumer. This way the company is doing its best to act as environmental ethically as possible.
- Liability
Companies willing to create and sell a product will have to confront to the liability of their product at a certain point.
Liability is the legal aspect of the product, preventing the company to be sued for damages or incidents created by their product or its use.
In order to avoid any issues concerning liability with the product, the company decided to comply with the following EU directives:
- Machine Directive (2006/42/CE 2006-05-17) [82]
- Electromagnetic Compatibility Directive (2004/108/EC 2004 12 15) [83]
- Low Voltage Directive (2014/35/EU 2016-04-20) [84]
- Radio Equipment Directive (2014/53/EU 2014-04-16) [85]
- Restriction of Hazardous Substances (ROHS) in Electrical and Electronic Equipment Directive (2002/95/EC 2003-01-27) [86]
Since Waste To Fungi delivers a service allowing to grow food, that would be eaten after growth, it is necessary to make sure to comply with existing food directives in Portugal in order to avoid any case of food poisoning.
Waste To Fungi decided to create a manual explaining how to properly use the product, protecting itself from incidents caused by wrongful use of the product. The decision has been made to choose trustful suppliers in order to minimize the risks of failures and potential liability issues.
- Conclusion
After precisely dealing with the ethical challenges, Waste To Fungi is even more determined to respect all the aspects mentioned regarding ethical behavior. While further developing the product the company will be conscious about treating employees and customers as well as the environment as ethical as possible. The main concern is the environmental ethics as Waste To Fungi strives to provide a completely circular service in which almost no waste will be produced and the local economy will be supported. The company will even go further and use “waste” as the main component of the product. This way it won’t only be avoided to produce any waste but also contributed to making a new purpose out of someone else's.
In the following chapter, Project Development is presented.
- Project Development
- Introduction
With a better understanding of the available solutions to the problem and the scientific field in which the organization is inserted (state of art), the market analysis as well as all ethical and sustainability considerations, it is necessary to develop a functional prototype as proof of the concept, as well as an analysis of the feasibility of the service proposed. This chapter aims to provide a better understanding of the entire development process of this project, going from an overview of the structure of the system to the closest of the final product/service as possible.
In that sense, the development of this project can be divided into two sections:
- Service development
- Product development
- Service development
Because the business is based on using coffee waste to grow mushrooms, Waste to Fungi needs an abundance of coffee waste. This is where the first part of the service comes into play. Waste to Fungi will act as collectors of coffee waste. This will involve providing cafes and restaurants with a container for them to put their daily coffee waste into which will be collected by runners employed by waste to fungi, this will then be delivered back to the production site where the coffee is mixed with mushroom spawn to make grow kits. Coffee waste needs to be fresh, so the service will involve daily collection. In exchange for providing ‘waste to Fungi’ coffee waste, the cafes and restaurants will be given a sticker to put in their window which shows that they are supporters of a sustainable business. The business intends to generate profit by offering 3 sizes of grow kits (1lL, 3L and 5L). Growkits will be made and incubated on site. Once the mycelium has fully colonised, they can then be sold to consumers, where they can grow fresh mushrooms at home. Any excess grows kits which are not sold, to avoid wasting them, they will be used directly by Waste to Fungi to grow fresh oyster mushrooms which can then be sold on the local market. The circular nature of the service described above is illustrated in Figure 18:

Waste to Fungi would also like to offer customers a subscription pack where they pay a monthly fee in exchange for discounts on all the products and workshops. They will also have access to information and resources. Information available will include full instruction on cultivation process including tips and tricks, nutritional value of specific mushroom, recipes, information on other sustainable food systems and access to a cultivation forum. All of this will be integrated into an app. The business also intends to make a profit by creating workshops about cultivating mushrooms and other sustainable food systems. Once the business is established and recognised in the local community, a small fee can be charged for coffee waste collection in return they can advertise themselves as a supporter of a sustainable solution.
- Drafts and Conceptualisation of the product
The design proposed in this chapter is a result of an analysis of different approaches to better solve the problem in question, starting with a “map of concept” (Figure 19 ) relating all relevant ideas, in that way facilitating the understanding of which solutions are the most efficient and effective.

After breaking the cultivation process into stages, the team looked for areas within the process that could be optimized to be made either more efficient or more environmentally friendly by reducing waste. Another area that was looked into was if the process could be simplified for growers at home. Despite a mushroom farm being quite sustainable as it is, there were key areas that let the process down. There seemed to be quite a lot of single-use plastics being used which could easily be substituted for more durable solutions. A conclusion was made that a low cost and simple solution was missing for users who wanted to grow at home on an adjustable scale which was not too cost and labor intensive.

A potential solution was defined in this section. Instead of using grow bags which would only be used once, why not use buckets to grow mushrooms. Buckets are much more durable and can easily be reused. Buckets come in a range of sizes and can easily be stacked for a modular cultivation process. Recycled buckets could be used and reused to adopt a more circular approach instead of a more traditional linear process by which the grow bags are used and then disposed of. The grow buckets can be accompanied by a modular fruiting chamber that not only allows the growing scale to be modular but allows growing conditions to be optimized and controlled to maximize harvest yields.

The chamber can automate the conditioning of the buckets by means of sensors and actuators thus making the entire growing process much easier for the costumer. The design also uses a spring to mount the grow bag. This makes it very easy to fold away for storage or transportation.
- Cardboard model
In Figure 22 a cardboard representation of the final product is presented.

- Solidworks model
In Figure 23 a rendered model of the product is presented.

- Substrate analysis
The substrate in which the Mycelium will be colonized to produce mushrooms will consist of 3 main components: Coffee Waste (which is free and will be collected from ISEP Cafeteria), Agricultural straw ( will be collected from a private source and will also be free) and lastly the most important the mushroom spawn. The Mushroom Spawn will have to be ordered from a spore producer. The specific spawn that the team is going to use is called Pleurotus ostreatus grain spawn. This strain was selected because it is well known for being easy to grow in coffee waste. There is a range of suppliers by which the spores can be ordered from both inside and outside Portugal. Since the team wants to be as environmentally friendly as possible while remaining economically sustainable too. The team needs to find a supplier which is as close as possible to minimize shipping costs and emissions. However, the team should also ensure that the price is right and that price is not compromised by choosing a supplier because they are closer. The team has decided to order from hortadomarao mushroom supplies because they are the closest while remaining price competitive with other suppliers.
- Substrate mix list
Nr | Component | Supplier | Price per Unit [€] | Quantity | Total Price [€] |
---|---|---|---|---|---|
1 | Spawn Pleurotus Ostreatus | Bioinvitro | 5.50 | 1 kg | 5.50 |
2 | Agricultural Straw | Loja Agropecuaria | 3.45 | 1 pack | 3.45 |
3 | Coffee | Restaurants and coffee shops | N/A | 2 kg | FREE |
Full Price : 8.95 € |
---|
- Materials analysis
- Buckets material
The bucket that will be chosen for the colonization of the mushrooms must have 3 features:
- The bucket should be made of a clear material to be able to track the colonization process.
- The bucket must be made of either a recyclable material or an organic material.
- The bucket must be made of a food grade material since food will be grown inside of it.
The solution found by the team consists of reusing packaging of products such as lupine seeds, or other food widely consumed in Portugal, which is usually conserved in clear buckets made out of PE or PP as shown in Figure 24.
This solution has two main benefits, it reuses waste and allows the business to diminish the costs.
The collection of such buckets could be made in restaurants and cafeterias, in order to have buckets of sufficient size.

- Chamber materials
The design of the chamber is made in order to have easy storage and modularity, allowing to fold the material in a minimal space when it is not being used. The chamber will be composed of the components described in this section to realize the first prototype.
- Spring solutions comparison
For the spring to be built, the team would need to shape a plastic or metal tube. Taking in consideration the equipment and scale actually considered, it was decided to use something already available on the market: a pop-up garden bag.
The different pop-up garden bags available on the market are depicted in table 18
Size | Material | Supplier | Price [€] |
---|---|---|---|
54×66 cm (150 L) | PE | Leroy Merlin | 5.99(pick up at the store) |
90 L | Unspecified | Manutan | 12.92 |
40×50 cm (60 L) | Unspecified | Planetahuerto | 9.90 |
- Transparent fabrics comparison
In order to obtain optimal parameters for growing, the mushroom needs to receive indirect light, in order to achieve that it was decided to have half of the tent opaque and the other clear using a clear fabric.
The different clear fabrics available on the market are depicted in table 19.
Thickness | Dimensions | Material | Supplier | Price [€] |
---|---|---|---|---|
0.25 mm | 1 x unspecified m | PVC | AKI | 3.99(pick up at the store) |
Unspecified | 5×2 m | PE | Leroy Merlin | 4.99(pick up at the store) |
- Sewing threads comparison
To assemble the whole, the solution that appeared as the best is the use of a sewing thread, as it would enable various assembling patterns and allow an easier reparation of the product. The goal for this part is to be durable and biodegradable, a cotton thread will then be used. There is no comparison for this component as it has no need for specific features, the provider will be the supervisors.
- Assembling system discussing
As modularity was an essential criterion for the team, the use of either Velcro tape or zippers came as an option. Those would allow to close and open easily the system, it would also allow us to achieve the expected modularity.
The first overview of prices and availability of products showed that Velcro would be a better option. Indeed Velcro would be easier to repair or replace, and it is more in accordance with the model of reusing tents after ones use.
The different velcro tapes available on the market are depicted in table 20.
Width | Length | Material | Supplier | Price [€] |
---|---|---|---|---|
20 mm | 2 m | Nylon | Printepoupe | 5.78 |
20 mm | 1.5 m | Nylon | AKI | 4.49(pick up at the store) |
20 mm | 3 m | Nylon | Leroy Merlin | 5.67(pick up at the store) |
- Full chamber material list
Nr | Component | Supplier | Price per Unit [€] | Quantity | Total Price [€] |
---|---|---|---|---|---|
1 | Pop up bag | Leroy Merlin | 5.99 | 1 | 5.99 |
2 | Velcro tape | Leroy Merlin | 5.67 | 3 m | 5.67 |
3 | Transparent fabric | Leroy Merlin | 4.99 | 1 | 4.99 |
4 | Sewing thread | Riera Alta | 1.30 | 1 | 1.30 |
Full Price : 17.95 € |
---|
- Chamber eletronic design
This chapter is intended to provide a conceptual description of the structure and behaviour of the eletronic system of the chamber.
- Architecture
For the chamber is idealized a system that can accurately read the temperature and humidity, and through those values, automatically maintain the chamber in the right condition for mushroom cultivation. The described system can be represented in terms of its inputs and outputs (Black Box Diagram), as shown in Figure 25.
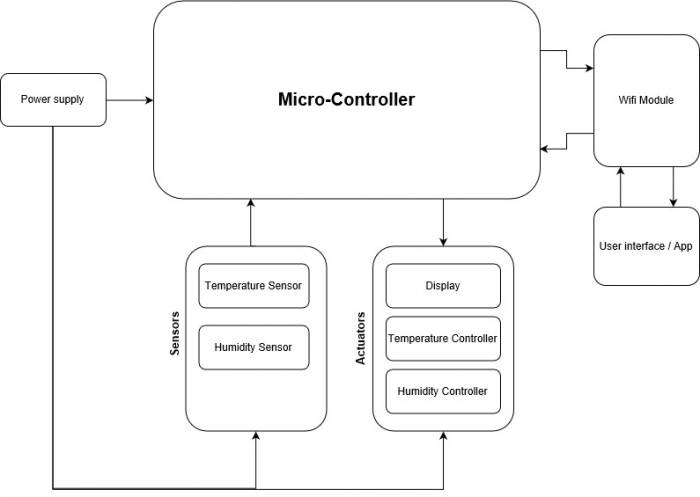
Power supply: A power supply is a device that supplies electric power to an electrical load. The most important aspect when selecting a power supply is the provided voltage and current (power).
Sensors: A sensor is a device that can convert a specific physical/chemical stimulus into another physical quantity (for example an electrical stimulus (voltage, current, resistance, etc)) usually for measurement and/or monitoring purposes. When selecting a sensor is important to take into consideration the accuracy and sensibility, as well the power consumption of the sensor.
Actuators: An actuator is a component responsible for controlling a mechanism or system. When selecting an actuator is important to take into consideration the effectiveness of activating the intended mechanism as well as the power consumption of the actuator.
Micro-Controller: The micro-controller is the “brain” of the system responsible for processing the signals received by the sensors and activating the actuators. There are several aspects to consider when selecting a microcontroller, from the number of pins to the processing power. For this project, in which does not require much processing capacity, the most relevant aspects to consider will be the operating voltage, and the number of pins as well as the ease to associate with modules and other peripherals.
In the following chapter, a more detailed comparison of the possible components and materials will be provided.
- Components
- Prototyping Boards Comparison
In Figure 22 a list of the considered prototyping boards is shown.
Prototyping Boards | Price [€] | Input Voltage [V] | Operacional Voltage [V] | Analog In/Out | Digital In/Out | USB Connection | Wi-Fi | Bluetooth | Supplier |
---|---|---|---|---|---|---|---|---|---|
Espressif ESP32 DevKitC [88]![]() | 8.73 | 3.3 to 5 | 3.3 | 16 | 32 | Micro | Yes | Yes | Mouser |
Arduino Nano V3.0 [89]![]() | 12.90 | 7 to 12 | 5 | 8 | 14 | Mini | No | No | Eletrofun |
Wemos D1 R2 ESP8266 [90]![]() | 18.70 | 9 to 24 | 3.3 | 1 | 11 | Micro | Yes | No | Eletrofun |
LoRa SX1278 display OLED 0.96 ESP32 [91]![]() | 24.90 | 7 to 12 | 5 | 18 | 28 | Micro | Yes | Yes | BotnRoll |
In case of using a micro-controller without a wireless connection integrated, a external wifi/bluetooth module is necessary. In Table 23 some options for those modules are presented.
When selecting a prototyping board there are several aspects that should be taken into account such as: internal memory, clock speed, processing speed, among others, but due to the simplicity of the project control system presented here, these will not be the factors more relevant to be taken into consideration during the comparison (all boards presented meet these minimum requirements), instead, they will be mainly valued by their operational voltage, ease of association with other peripherals and price, the latter having the biggest influence in the decision.
With that said the prototyping board “Espressif ESP32 DevKitC” was selected. The team believes that this is the best choice for its easy integration with external peripherals, the huge amount of online resources about its funcionalities, the fact that it already has an integrated wifi module and most importantly for having the best cost / benefit ratio of all solutions presented.
- Temperature and humidity sensors comparison
Temperature and humidity sensor comparison in Table 24.
Model | Price [€] | Input Voltage [V] | Current [mA] | Temperature Range [°C] | Temperature Accuracy [°C] | Humidity [%] | Humidity Accuracy [%] | Supplier |
---|---|---|---|---|---|---|---|---|
DHT11 [94]![]() | 4.15 | 3.3-5 | 3-4 | 0-50 | +-2.0 | 20 - 90 | +-4 | Eletrofun |
DHT22 AM2302 [95] ![]() | 12.30 | 3.3-5 | 2.5 | -40 - +80 | +-0.5 | 0 - 100 | +-3 | Eletrofun |
HTU21D-F [96] ![]() | 13.93 | 1.5-3.6 | ± 0.5 | -30 - +90 | +-1 | 5 - 95 | +-2 | Mouser |
With the purpose of delivering the most quality for the client, the team selected the temperature and humidity sensor “HTU21D-F” because despite being the most expensive sensor is also the most accurate one (the price difference is not very significant) and also uses the same operacional voltage as the previous selected prototyping board.
- Servo Motors Comparison
Servo motors comparison in Table 25.
The servo motor will be coupled to a spray mechanism that will regulate the humidity in the air, in that sense, a servo motor with significant torque power is necessary. Of all the options considered, the servo motor MG996R is the most indicated because of its high torque, as well as already had been used in similar mechanisms [100].
- Power supply calculation
In Table 26 the power calculations are being shown.
Component | Quantity | Voltage [V] | Current [mA] | Power Consumption [mW] |
---|---|---|---|---|
Servo Motor MG996R | 1 | 5 | 2500 (max) | 12500 (max) |
Espressif ESP32 DevKitC | 1 | 5 | 200 (absolute max) | 1000 |
Fan | 2 | 12 | 110 | 2640 |
DHT22 AM2302 | 2 | 3.3 | 2.5 | 16.5 |
Heater (power resistors) | 2 | 12 | 214 | 5143 |
Total Power consumption: 21 299.50 mW |
By this calculation any power supply with a 21 299.50 mW or higher power is sufficent to power the entire circuit. Thus the power supply selected is shown in Table 27:
Component | Price [€] | Supplier | Voltage [V] | Current [mA] | Max power provided [mW] |
---|---|---|---|---|---|
Adaptor/Charger AC/DC 12 V | 6.30 | Eletrofun | 12 | 2000 (max) | 24000 (max) |
- Complementary components
In addition to the components already mentioned above, some control elements are still necessary, which do not require much comparison (the cheapest one that meets the needs is chosen), but are very important for the proper functioning of the circuit. Listed below are some of these elements:
- Resistors
- Transistors
- Capacitors
- Diodes
- LED
- Wires
- ON/OFF Switch
- Voltage Regulator
- Full Eletronic Components List
In Table 28 the full electronic components list is shown.
Nr | Component | Supplier | Price per Unit [€] | Quantity | Total Price [€] |
---|---|---|---|---|---|
1 | Humidity And Temperature Sensor Module DHT22 AM2302 | Electrofun | 12.30 | 2 | 24.60 |
2 | Breadboards | Eletrofun | 6.00 | 2 | 12.00 |
3 | MG996R Servo Motor | Eletrofun | 8.95 | 1 | 8.95 |
4 | Wemos D1 R2 Placa Wi-Fi ESP8266 | Electrofun | 18.70 | 1 | 18.70 |
5 | Adaptor/Charger AC/DC 12 V | Eletrofun | 6.30 | 1 | 6.30 |
6 | Wires male-male | Eletrofun | N/A | 65 | 4.10 |
7 | DC Power Cable Female Jack 25 cm ProK | Eletrofun | 1.50 | 1 | 1.50 |
8 | Transistor TIP120 NPN | Eletrofun | 0.49 | 3 | 1.47 |
9 | 56 Ω / 5 W Ceramic Resistor 588-TUW5J56RE | Mouser | 0.66 | 2 | 1.32 |
10 | 2 Pins buttons for painels SPST ON-OFF 15 mm | Eletrofun | 0.95 | 1 | 0.95 |
11 | Voltage Regulator LM1086CT-3.3 / NOPB | Mouser | 1.62 | 1 | 1.62 |
12 | Voltage regulator 7805 5 V | Eletrofun | 0.50 | 1 | 0.50 |
13 | 100 nF Capacitor | Eletrofun | 0.10 | 3 | 0.30 |
14 | Diode 1N4007 | Eletrofun | 0.10 | 2 | 0.20 |
15 | 680 Ω Resistor | Eletrofun | 0.05 | 3 | 0.15 |
16 | Red LED | Eletrofun | 0.14 | 1 | 0.14 |
17 | 1 uF / 50 V Capacitor | Eletrofun | 0.10 | 1 | 0.10 |
18 | 8.2 kΩ Resistor | Eletrofun | 0.05 | 1 | 0.05 |
19 | 10 kΩ Resistor | Eletrofun | 0.05 | 1 | 0.05 |
20 | 12V Fan EC8025M12EA | Farnell | 2.72 | 2 | 5.44 |
21 | Printed Circuit Board Perforated Simple Face 160x115mm | botnroll | 3.25 | 1 | 3.25 |
Full Price : 91.69 € |
---|
- Price Analysis
The team compared different materials and components needed for building the prototype. Selection was made based on characteristics, availability and price. All the chosen components and their price, as well as total cost of the prototype is shown in Table 29.
Nr | Component | Supplier | Price per Unit [€] | Quantity | Total Price [€] |
---|---|---|---|---|---|
Electronic components | |||||
1 | Humidity And Temperature Sensor Module DHT22 AM2302 | Electrofun | 12.30 | 2 | 24.60 |
2 | Breadboards | Eletrofun | 6.00 | 2 | 12.00 |
3 | MG996R Servo Motor | Eletrofun | 8.95 | 1 | 8.95 |
4 | Wemos D1 R2 Placa Wi-Fi ESP8266 | Electrofun | 18.70 | 1 | 18.70 |
5 | Adaptor/Charger AC/DC 12 V | Eletrofun | 6.30 | 1 | 6.30 |
6 | Wires male-male | Eletrofun | N/A | 65 | 4.10 |
7 | DC Power Cable Female Jack 25 cm ProK | Eletrofun | 1.50 | 1 | 1.50 |
8 | Transistor TIP120 NPN | Eletrofun | 0.49 | 3 | 1.47 |
9 | 56 Ω / 5 W Ceramic Resistor 588-TUW5J56RE | Mouser | 0.66 | 2 | 1.32 |
10 | 2 Pins buttons for painels SPST ON-OFF 15 mm | Eletrofun | 0.95 | 1 | 0.95 |
11 | Voltage Regulator LM1086CT-3.3 / NOPB | Mouser | 1.62 | 1 | 1.62 |
12 | Voltage regulator 7805 5 V | Eletrofun | 0.50 | 1 | 0.50 |
13 | 100 nF Capacitor | Eletrofun | 0.10 | 3 | 0.30 |
14 | Diode 1N4007 | Eletrofun | 0.10 | 2 | 0.20 |
15 | 680 Ω Resistor | Eletrofun | 0.05 | 3 | 0.15 |
16 | Red LED | Eletrofun | 0.14 | 1 | 0.14 |
17 | 1 uF / 50 V Capacitor | Eletrofun | 0.10 | 1 | 0.10 |
18 | 8.2 kΩ Resistor | Eletrofun | 0.05 | 1 | 0.05 |
19 | 10 kΩ Resistor | Eletrofun | 0.05 | 1 | 0.05 |
20 | 12V Fan EC8025M12EA | Farnell | 2.72 | 2 | 5.44 |
21 | Printed Circuit Board Perforated Simple Face 160x115mm | botnroll | 3.25 | 1 | 3.25 |
Chamber materials | |||||
1 | Pop up bag | Leroy Merlin | 5.99 | 1 | 5.99 |
2 | Velcro tape | Leroy Merlin | 5.67 | 3 m | 5.67 |
3 | Transparent fabric | Leroy Merlin | 4.99 | 1 | 4.99 |
4 | Sewing thread | Riera Alta | 1.30 | 1 | 1.30 |
Substrate mix | |||||
1 | Spawn Pleurotus Ostreatus | Bioinvitro | 5.50 | 1 kg | 5.50 |
2 | Agricultural Straw | Loja Agropecuaria | 3.45 | 1 pack | 3.45 |
Full Price : 118.59 € |
---|
- Detailed Schematic
In order to achieve the previously stated objective (having a system capable of maintaining the chamber temperature and humidity in the appropriate range) the team used the schematic shown in Figure 26.
In agreement with the BlackBox diagram presented at the beginning of the product development section, the system must be able to accurately read values of temperature and humidity inside the chamber, processing them and if necessary acting to keep them in the desired range.
- To read the temperature and humidity values, the DHT22 sensor is being used.
- To process the data read, the Wemos D1 R1 (has a WiFi module builtin) prototyping board is being used.
- In terms of actuators are being used: two fans, two power resistors and one servo motor.
A more detailed explanation of the system operation will be presented in the next section.
- Software Development
With the schematic presented in the previous section we have the fundamental hardware for the intended system. This chapter aims to give a better understanding of the software behind the system.
- Monitoring software
The DHT22 sensor uses three main components: a humidity sensor, an NTC temperature sensor (thermistor) and an IC to facilitate communication with the microcontroller. (As shown in Figure 27)

- To read the humidity, the sensor consists of two electrodes with a substance that retains moisture between them, so when the humidity changes the resistance between the two electrodes changes, ie there is a variation in conductivity between the two subtances this change in the conductivity is processed by the IC and later read by the micro-controller (As shown in Figure 28).

- To read the temperature a thermistor is used. A thermistor is a component whose resistance varies according to temperature. Normally these sensors are made by sintering of semiconductive materials such as ceramics or polymers in order to provide larger changes in the resistance with just small changes in temperature. The term “NTC” means “Negative Temperature Coefficient”, which means that the resistance decreases with increase of the temperature (As shown in Figure 29).

Currently there is a large variety of libraries that facilitate reading these values, the team used the libraries: “DHT.h” and “Adafruit_Sensor.h” for Arduino.
Moreover, for the connection of the micro-controller to the cloud, a ThingSpeak channel is being used. According to its creators “ThingSpeak is an open-source Internet of Things (IoT) application and API to store and retrieve data from things using the HTTP protocol over the Internet or via a Local Area Network. ThingSpeak enables the creation of sensor logging applications, location tracking applications, and a social network of things with status updates ” [104].
The connection to ThingSpeak servers is really easy due to the large number of online libraries and resources available that hide the complexity of the protocols used, the team used the libraries: <ESP8266WiFi.h> and <ThingSpeak.h> for Arduino.
That way the team was able to read the DHT22 sensor values and send/store them on a ThingSpeak channel.
- Actuating software
The system must be able to act in three ways:
- Cool
- Warm
- Increase humidity (due to the use of fans the humidity is constantly being reduced)
- Cooling (Increase air circulation)
For the control/regulation of the temperature and humidity of the chamber several strategies were thought:
The first strategy consisted on using two DHT22 sensors (one outside the chamber and the other inside), and two fans (one at the bottom of the chamber and one at the top). The data from both sensors would be read and if the outside temperature was lower than the interior, the fans would circulate fresh air inside the chamber (the chamber being a closed system) thereby reducing the chamber's inside temperature.
For a big part of the project this was the strategy the team wanted to implement, but it failed in many aspects:
- Except for some less common situations, with the chamber closed, the temperature inside the chamber would differ too much from the ambient temperature. (so the use of a second sensor would be almost redundant).
- The temperature inside the chamber could never be lower than the ambient temperature, so the chamber would always have to be in an environment with, initially, low temperatures (thus reducing the relevance of having a cooling system), or associated with one of the fans should be a source of fresh air (bucket with ice or some more sophisticated solution like a compressor), which would increase the cost of the prototype.
- There is a higher cost due to the use of two DHT22 sensors.
Therefore, it would require more hardware solutions to achieve a reliable cooling system, so, the team focused on the using one DHT22 sensor to read the temperature and humidity inside, and two fans as a way of increasing air circulation inside the chamber.
- Warming
To heat the system, the team decided to use two power resistors associated with one of the fans. If it is necessary to heat the system the resistors will be heated and the fan will blow some air in order to spread the heat through the whole chamber.
- Increasing humidity
In order to increase the humidity of the system a servo motor has been associated with a sprinkling mechanism, so whenever the system needs to be humidified the servo motor is triggered and it is squirt water through the chamber. With the use of the fans this water is evaporated and the humidity of the air is increased.
An image and a video of the mechanism can be seen in Figure 30 and 31.
- Software description
Note:
During the fruiting phase the ideal internal temperature of the chamber must be between 18 °C - 22 °C, and the humidity between 40 % - 60 %, moreover for some extreme values of temperature (temperatures below 15 °C or temperatures above 25 °C), because of the scale of the project the system wouldn't be effective on regulating those values, so on those cases a message should be send to the user to move the chamber to another place.
temp_in - Temperature inside the chamber
hum_in - Humidity inside the chamber
TEMPMIN_C - Minimum temperature that is worth using the fans (21 °C)
TEMPMAX_C - Maximum temperature that is worth using the fans (25 °C)
TEMPMIN_H - Minimum temperature that is worth using the heater (15 °C)
TEMPMAX_H - Maximum temperature that is worth using the heater (19 °C)
HUM_MIN - Minimum humidity that is worth using the humidifier (60 %)
The main program (which will run in a constant loop) works as shown in the following flowchart (Figure 32):
The humidifying function works as shown in the following flowchart (Figure 33):
The heating function works as shown in the following flowchart (Figure 34):
The cooling function works as shown in the following flowchart (Figure 35):
The team aims that with the system described above it will be possible to increase the airflow (and reducing slightly the temperature) and be able to maintain the humidity in the right range, thus facilitating the fruiting process of the mushroom. Moreover in the future, in support of the costumer, with external communication (via Wifi) is intended to present relevant information on mushrooms growth, via a mobile App, such as: nutritional value, curiosities, among others. In addition to this, it will be possible to collect data from these sensors and, through statistical methods, over time, produce studies on the optimization of the cultivation of this type of mushrooms.
The next chapter will focus on the tests and obtained results.
- Tests and Results
- Cultivation Process tests
The results of the first batch of buckets are still ongoing. Despite all the buckets having a good start, there were some issues with the internal humidity of the bucket being too high from the 3rd to the 12th-day of recordings as can be seen in Figure 37. This alongside with an increase in temperature around day 9 to day 12 as displayed in Figure 36, might have allowed contamination to spread in some of the buckets. Contaminated buckets were isolated and observed so the contamination could be identified and diagnosed. One of the control buckets in which the substrate was not pasteurized showed early sign of Green mold. This was most likely caused by the waste coffee used not being fresh and was already contaminated. Many of the buckets were contaminated with Neurospora. The pasteurized substrate facing humidity and a temperature increase alongside with too low ventilation allowed Neurospora to quickly appear on various buckets. The team had much more success with the buckets that used coffee waste that had not been pasteurized. This might be because by pasteurizing the substrate creates a better and more neutral environment for the Neurospora to thrive. Increase in temperature came down to weather and poor ventilation in the initial incubation site. The team then decided to move the incubation site to a new area with better ventilation, allowing the temperature and humidity to remain in an appropriate range. Temperature and humidity are carefully being monitored with the monitoring system developed by the team, alongside daily visual inspections. The team has started a second batch of smaller buckets with a slightly refined process alongside with much stricter cleaning procedure. These changes are bringing promising results and the team will continue to document the cultivation process. The Table 30 depicts pictures and comments of the inoculation process of the team's first batch.
In figure 36, the temperature of the growing medium is displayed. The team recorded the values for a month, starting from the 15th of May and ending on the 14th of June. On the weekends, no measurements were made and therefore not implemented in the chart. On the y-axis, you can see the temperature in °C, on the x-axis the days of recording. Temperature rise was recorded on the 10th day until it reached its peak at almost 25 °C on the 12th day. This is the only time the critical point for temperature was reached and passed. Due to this incident, the team decided to change the cultivation to another location to avoid this happening again. Resulting in better temperature control, and temperature remaining safely in the defined range.
In figure 37, the humidity of the growing medium is displayed. The team recorded the values for a month, starting from the 15th of May and ending on the 14th of June. On the weekends, no measurements were made and therefore not implemented in the chart. On the y-axis, you can see the relative humidity in %, on the x-axis the days of recording. In the first days, it stayed in the recommended range at around 80 %. It reached a peak on the 12th day of recording but did not reach the high critical point. The team then decided to change the growing environment to have better control of the temperature and humidity. Resulting in better humidity control, considering that humidity remained at around 75%.
Fruiting Results -Below you can see the teams first bucket through out its first fruiting flush.
Despite having a very good start into the fruiting process. The team had issues with temperature and air circulation. There was an increase in temperature due to weather, therefore the team decided to increase air circulation using the fans however with the fan constantly blowing the chamber dried out very quickly which temporarily stunted the growth of the mushrooms. This lead to the mushrooms drying out. The team has documented and learnt from this and is adapting the chamber accordingly to achieve ideal fruiting conditions. Fans will only come on for short intervals to removed old air instead of constantly blowing, preventing the chamber and the mushrooms from drying out.
- Chamber prototyping tests
In order to ensure the proper functioning of the final prototype, several tests must be performed. The methodology behind the testing will be based on trial-and-error, which means that the code will be tested, in case of error debugged and tuned, until the desired results are achieved, which in this case is for the chamber prototype to be able to maintain all the proper theoretical conditions for mushroom cultivation.
- Hardware Test
These tests have the intent of ensuring that all of the following components are working properly. All videos of test runs can be found in a file named: “test.zip” in the deliverables section.
Sensors (DHT22)
The test was performed by comparing the value read by the sensors to those of an external/calibrated sensor as can be seen in Figure 39.
The tests will be successful if the temperature read on the sensors that are being used doesn't differ more than 2 - 3 % [105] from that read by an external/calibrated sensor.
Fans
To test the fans a simple program was run on it to ensure that they are working properly.
The program consisted of incrementally increasing the speed of the fans during 5 seconds, after that stop, both fans, wait five seconds and restart the program, as can be seen in Figure 40.
For the test to be successful the fans have to perform the mentioned program.
Power resistors
For testing the power resistors, the team used an ohmmeter to measure each resistor resistance and that way ensure that they're within the allowed range (specified by the manufacturer), as can be seen in Figure 41. For this test to be successful the value read with the ohmmeter shouldn't differ more than 5% to 55kohm.
Servo motor (MG996R)
A simple program was run on the servo motor to ensure that it was working properly.
The program consisted of switching between two positions constantly, as can be seen in Figure 42. For the test to be successful the servo motor has to perform the mentioned program.
- Software tests
Prototyping board Wi-Fi board ( ESP8266) and ThingSpeak connection
As a way of testing the connection between the prototyping board and the ThingSpeak server, random numbers were generated and sent to the server. As can be seen in Figure 43.
For the tests to be successful, the generated values must be represented in the online graphics.
- Prototype tests
The testing of the prototype was performed in three instances:
Monitoring of temperature and humidity in “ideal conditions”
The prototype was placed into the setup shown in Figure 44. In that set up the entire system is within a low light room with a relatively low temperature (18 ºC - 23 ºC), a bucket with water is being used to keep the humidity in the ideal range.
The objective is to check if the system can properly monitor the temperature and humidity of the place.
The tests started on 2019-06-08 at 16:17:20 in Braga, Portugal and finished on 2019-06-09 at 10:34:22 in Braga, Portugal. The team managed to keep track of the proposed parameters for about 17h, as can be seen in Figure 45, 46 and 47. Further results can be found in “Moni_Results_CSV” file in the deliverables section.
With the data acquired is possible to infer that the “place” monitored could be adequate for mushroom cultivation (temperature in the range of 18 ºC to 22 ºC, and humidity between 40% and 60%).
System in the chamber
Finally, the whole system was assembled in the chamber (Figure 48) to see if with help of the actuators the temperature and humidity can be maintained within the ideal range.
A video of the prototype working can be seen in Figure 49
During this test phase, due to problems in the prototyping board it was necessary to change it, and the new one that was being powered by the voltage regulator 12 V - 5 V, which was feeding simultaneously the servo motor and the prototyping board, could not provide sufficient current to the board, so the tests described here had to be performed with the board fed by a USB cable connected to the computer, furthermore impeding the closure of the protective case.
The results of the tests can be found in Figure 50 and 51.
With the data obtained here it was possible to verify that the actuators used are not sufficient to effectively maintain the temperature in the desired range, being able to only decrease the temperature in the chamber by 0.5 ºC (almost insignificant, as speculated in the previous chapter), however, the system has been successful in maintaining air circulation inside the chamber, which helps reducing the moisture indexes (one of the biggest problems during the cultivation process).
- Results table
Results | ||||
---|---|---|---|---|
Functionality | Requirement | Test | *Success rate | Note |
General project requirements | ||||
Develop a low-cost solution that fits all requirements. | Budget for entire project should not exceed 100 euros. | Check through receipts and check whether costs have exceeded the budget. | 2 | The prototype developed did not fulfil all the requirements initially established, the team was able to design a prototype that met the monetary requirements suggested, but the project presented here had a slightly higher cost than initially planned. |
Design should be modular | Scale of cultivation should be adjustable based on consumer needs. | Test whether scale can be adjusted and whether or not system supports larger scales. | 2 | The team was able to achieve modularity in relation to the arrangement of the components in the chamber, however the modularity of the chamber with other chamber was not tested because the team only had one chamber. |
Grow kit | ||||
Colonise coffee waste with mycelium. | Fully colonise grow bucket without contamination. | Daily visual checks. Bucket should be completely white! Check for contamination. | 3 | N/A |
Grow Mushrooms using colonised buckets. | Cultivate at least 500grams per colonised bucket. | Weigh Harvest after each flush. | 3 | N/A |
The plastic bucket should be reusable. | Bucket should be reused at least 5 times. Must be easy to clean. | Visual checks during and after each cultivation process. Check for damage and contamination. | 3 | N/A |
Chamber prototype | ||||
The temperature and humidity inside the chamber can be monitored and the values stored in a cloud server (ThingSpeak channel) | The temperature and humidity should be monitored for long periods of time. The data acquired should be visualised in a public ThingSpeak channel and be downloadable for the public. | During a period longer than 12 h monitor the temperature and humidity of chamber and store the values in a ThingSpeak channel. After the values should be visualised and the data downloaded by a public entity. | 3 | N/A |
The temperature and humidity inside the chamber can, by means of actuators, be maintained within the theoretical ideal range for mushroom cultivation | The temperature of the chamber can be maintained within the range of 18 ºC and 22 ºC, and the humidity within 40% - 60% during long periods of time. | Place the chamber in non-ideal conditions for mushroom cultivation and monitor the temperature and humidity inside the chamber to see if during a period of more than 12 h the chamber can maintain the temperature within the range of 18 ºC - 22 ºC and humidity within 40% - 60%. | 2 | with the tests carried out the team found that with the actuators at the disposal it is not possible to maintain the temperature within the desired range. For that, stronger fans would be needed, or a redesign of the system in order to get the desired results. Nevertheless, with the implementation of the fans the environment for cultivating the mushrooms is improved due to an increase in airflow |
The prototype can be used to help grow mushrooms | Over a period of 3 - 4 weeks the prototype should be able to guarantee the conditions so that the buckets colonised with mycelium can successfully fruit. | Put 3 buckets of colonised mushrooms, and for 4 weeks check every 2 days if mushroom are development properly. | Not performed | Due to the limited time available this test cloud not be performed. |
Success rate:
- 1 - The tests were not successful, and the obtained results do not allow to draw meaningful conclusions for the project.
- 2 - The tests did not have the expected results, but important conclusions could be drawn from them.
- 3 - The tests were successful, had the expected results and helped to draw important conclusions for the project.
- Conclusion
The project development started after defining the marketing idea of our project. The main target we defined was to create a product and service that would create as less waste as possible.
In order to create such a product, the team discussed different ideas, one of them being reusing the growing medium of our product. The team then decided to choose buckets, which is a widely available waste that could easily be repurposed to grow mushrooms, or recycled if broken. Around this bucket, a whole service was designed, it would allow the creation of a business within the frame of the circular economy.
The bucket is still actually being tested and the process around it improved. More specifically the hole covers used during the inoculation process need more research and tests to create a product more resilient to contamination, many options are still to be explored and tested. It would allow to improve the cultivation success rate. The teams cultivation process is still on going. The team is currently in the fruiting stage and is trying to optimize growing environment using the chamber to regulate its environment. This is still a learning process and the team is still trying to understand and refine the whole process. This is being done through documenting procedures and results and modifying techniques, which the results will then be analysed and implemented accordingly. The idea behind the grow chamber was to develop a product with features that would enable the customer to grow mushrooms at home effortlessly. This product had aimed to be modular, allowing a variety of growing containers to be fit in, and easily stored which has been made possible using a spring system. The electronics have been designed and develop in order to control the temperature and humidity of the growing medium and environment, this part still requires further development to be functional. The concepts can be implemented on both a small scale chamber for home cultivators but also a larger industrial scale such as a grow room that would most likely be used by the company.
Difficulties encountered were mainly time and budget. Creating a low scale mushroom farm was quite difficult in terms of electronics with the intended budget. Indeed regulating temperature and humidity, as well as other parameters on such a low scale can hardly be made effective for a low price. The time was a difficulty mainly that testing while using the whole system to improving the cultivation process, considering its biological nature that cannot be rushed was more difficult then intended and could have been over come with better planning and risk assessment.
Overall the results the team has faced weren’t as promising as what was expected but still allowed the team members to learn a lot and from this they can develop a more resilient and reliable process through continued experimentation which will results in a much higher quality product and surrounding service.
The next chapter will present the conclusions and prospective the team drew during this project.
- Conclusions
- Discussion
The team set out to test the feasibility of creating successful business surrounded the idea of using coffee waste to grow oyster mushrooms and to develop multidisciplinary skills that may prepare them for future employment. The team was able to create a marketing plan to promote the grow kit and the surrounding service to target consumers. A detailed business plan was created to specify logistics, costs and funding, supplies and target consumers. This allowed the team to fully specify the ins and out of the business to potential sponsors for future funding. In terms of the cultivation process, arguably the most important part, the team has made a good start in refining the process and are testing the concept. Despite some initial failures with contaminations the team is closer to understanding the process in much more detail and all the potential risks associated with the cultivation process. The team will continue developing and analysis a safe, reliable and repeatable process which will allow the cultivation of large yields of oyster mushrooms. The team would like to investigate potential sources of contamination in order to prevent risks in future cultivation and develop counter measures for prevention. The fruiting chamber was developed and prototyped, the functionality was tested however the team was not able to monitor the actual growing of the mushrooms due to contamination issues and time lags however the team is striving toward a successful cultivation of a fully colonised bucket of mycelium which can then be used to cultivate mushrooms inside the fruiting chamber which will allow the team to conclude their investigation into the cultivation process. Prospectively, to guarantee success the team would invite an expert to share some knowledge into optimising the cultivation process while eliminating risk. Another option would be to partly outsource the inoculating process, whereby the team would collect the raw materials to build the growing substrate, while an external company (with more expertise in the field) would inoculate and colonise the buckets. Once the buckets have been fully colonised the team would distribute the buckets to consumers. Collaborative work can be difficult, especially in a multi-cultural and multi-disciplinary context. One of the biggest challenges the team faced was time management while organising logistics and distributing tasks amongst the team members. The team worked with each member’s strengths which consolidated their own knowledge in the field while also developing many other skills in subjects such as marketing and sustainability. Soft skills such as organisation and communication were also practiced and developed. All the team members can agree that the EPS@ISEP was a very useful experience in not just personal development but also preparing them for future employment. Not to mention the whole experience allowed the members to explore Portugal and indulge into its rich culture.
- Future Development
During the project, the team had the opportunity to implement their own knowledge and skills into the project, enhancing the outcome. Nevertheless, due to time, budget restrictions and sometimes a lack of experience, the team was not able to develop its product to its full potential.
In order to be more efficient on this project the team would have liked to:
- Improve their planning by selecting a team manager, who would make sure tasks and requirements are met on time.
- Define and secure a room dedicated to Waste to Fungi allowing to work in an optimal environment for cultivation.
In order for the project to be fully functional the team would have like to develop more on the following aspects:
- Test various kinds of hole covers allowing airflow to reduce contamination risks.
- Develop a fully functional Inoculation chamber for production purposes.
- Develop an effective partnership with restaurants and coffee shops in Porto.
- Develop an application and the chamber further, if the need for it appears.
- Create a workshop scheme.